Geschätzte Lesezeit 69 Minuten
Predictive Maintenance − die Zukunft der Instandhaltung
Ungeplante Ausfälle von Maschinen und Anlagen führen branchenübergreifend zu kostspieligen Stillständen und Produktivitätseinbußen. Predictive Maintenance (PdM) bietet hier Abhilfe. Dieser Ratgeber beleuchtet, wie PdM funktioniert und welche technologischen Voraussetzungen notwendig sind, um es erfolgreich zu implementieren.
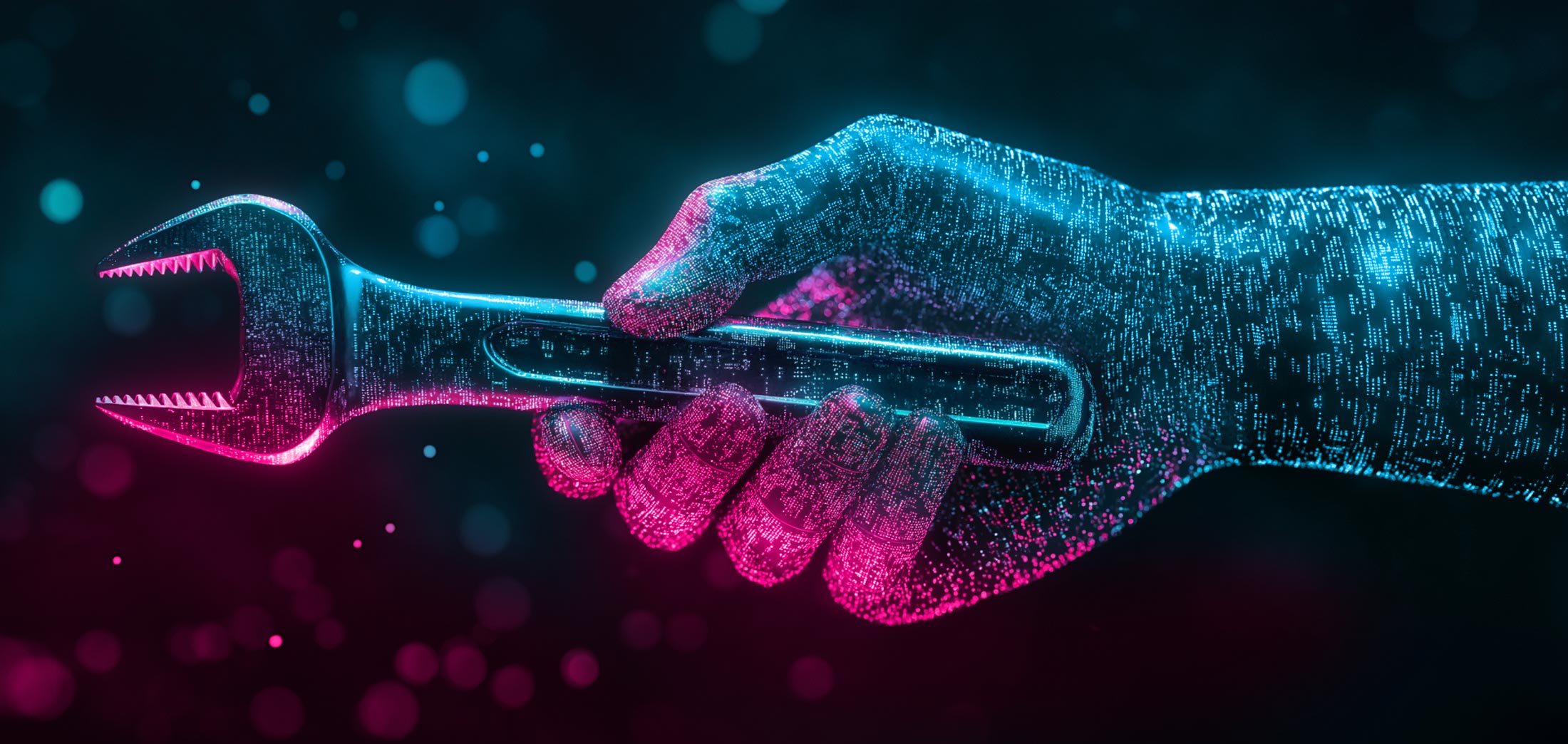
Overview
- Was genau ist Predictive Maintenance?
- Wie funktioniert Predictive Maintenance?
- Die technologischen Grundlagen
- Welche Vorteile bietet die vorausschauende Wartung?
- Welche Herausforderungen gibt es bei der Implementierung?
- Der Weg zur Implementierung von Predictive Maintenance
- Use Case – Predictive Maintenance für Remote Access
- Predictive Maintenance − Investition in die Zukunft
- FAQ: Häufig gestellte Fragen zur vorausschauenden Wartung
Ungeplante Ausfälle von Maschinen und Anlagen führen branchenübergreifend zu kostspieligen Stillständen und Produktivitätseinbußen. Predictive Maintenance (PdM) bietet hier Abhilfe.
Durch eine kontinuierliche Überwachung von Maschinen und Anlagen können Vorhersagen getroffen werden, wann Wartungsarbeiten erforderlich sind, bevor es zu einem Ausfall und im schlimmsten Fall zu einem Produktionsstillstand kommt. Doch wie funktioniert diese Methode und was ist nötig, um sie im Unternehmen zu implementieren?
Dieser Ratgeber beleuchtet, wie Predictive Maintenance funktioniert und welche technologischen Voraussetzungen notwendig sind, um es erfolgreich zu implementieren. Darüber hinaus werden die Chancen und Herausforderungen dieser Wartungsstrategie erörtert, mit einem besonderen Fokus darauf, wie Unternehmen durch gezielte Optimierung der Instandhaltungsprozesse ihre Effizienz steigern.
Was genau ist Predictive Maintenance?
Die Idee der vorausschauenden Wartung ist nicht neu. Bereits in den 1940er Jahren wurden in der Luftfahrtindustrie erste Konzepte entwickelt, um Ausfälle von Flugzeugen zu vermeiden. Doch erst mit dem Aufkommen von Industrie 4.0 und dem Internet of Things (IoT) wurde Predictive Maintenance zu einem Kernthema in der Instandhaltung.
Definition: Predictive Maintenance ist eine Methode zur Zustandsüberwachung von Maschinen und Anlagen, bei der Daten in Echtzeit erfasst und analysiert werden, um drohende Ausfälle frühzeitig zu erkennen und zu verhindern.
Traditionell wird in der Instandhaltung zwischen reaktiver und präventiver Wartung unterschieden. Bei der reaktiven Wartung werden Maschinen erst repariert, wenn sie bereits ausgefallen sind. Die präventive Wartung erfolgt dagegen in festen Intervallen, unabhängig vom tatsächlichen Zustand der Anlage. Beide Ansätze haben jedoch Nachteile.
Die reaktive Wartung kann langfristig zu höheren Kosten führen, da sie häufig den vorzeitigen Verschleiß von Komponenten und eine verkürzte Lebensdauer von Maschinen zur Folge hat.
Im Gegensatz dazu erfordert die präventive Wartung den Austausch von Teilen, die möglicherweise noch funktionsfähig sind, sowie die Implementierung komplexer Wartungsprogramme. Dieser Ansatz ist mit einem erhöhten Zeitaufwand verbunden und führt zu regelmäßigen Unterbrechungen der Produktionsprozesse.
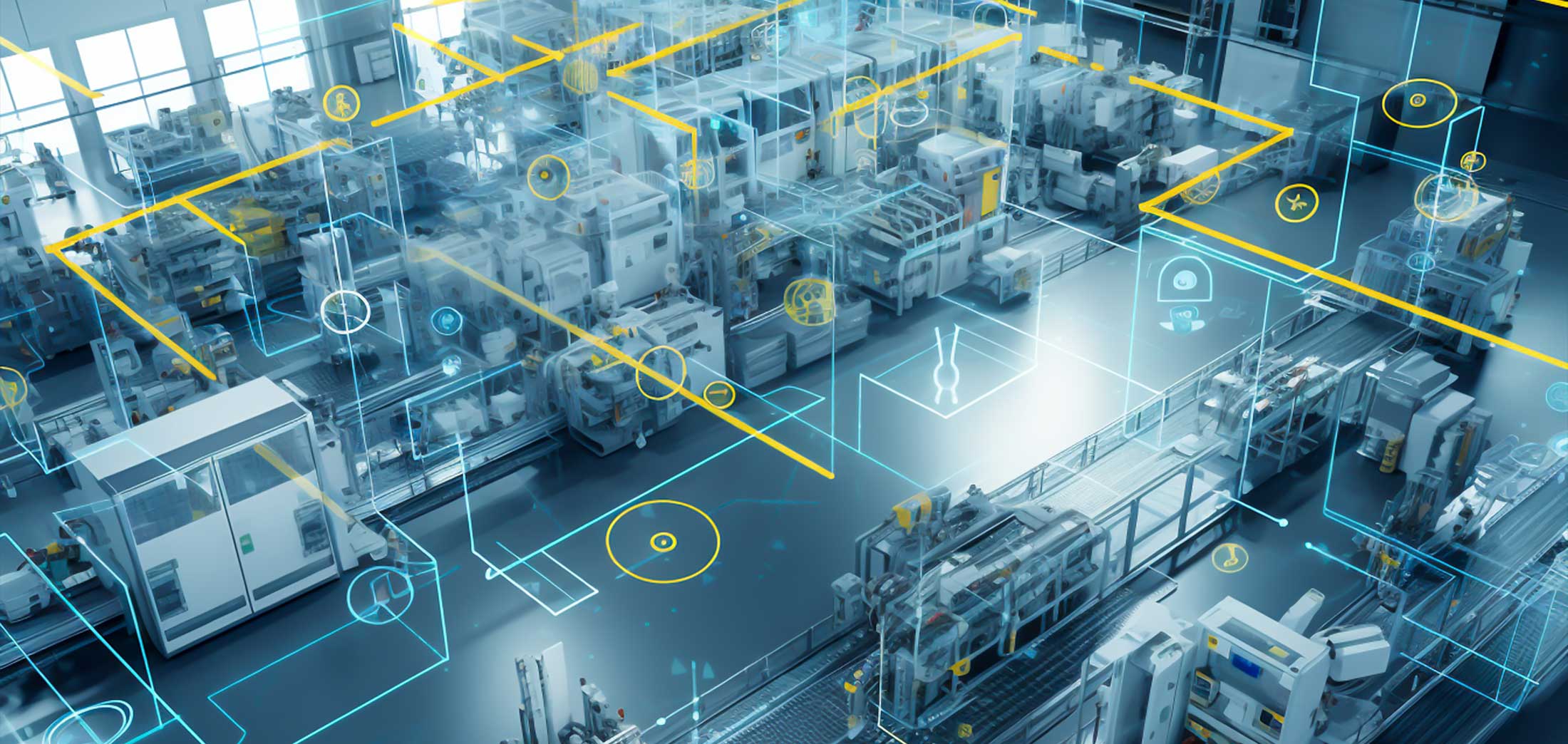
Prädiktive Wartung geht einen Schritt weiter. Durch den Einsatz von Sensoren und KI-gestützter Datenanalyse wird der optimale Zeitpunkt für Wartungsmaßnahmen ermittelt. Dies kombiniert die Vorteile beider Ansätze und minimiert deren Nachteile.
Ein Beispiel ist die vorausschauende Wartung von Werkzeugen bei Dreh- und Fräsmaschinen. Während eines Bearbeitungsprozesses verschleißt das Werkzeug und ab einem bestimmten Punkt können aufgrund der Abnutzung Vibrationen oder Rattern am Werkzeug entstehen. Diese Vibrationen führen zu weiteren Belastungen, bis das Werkzeug schließlich abbricht. Mithilfe von Sensoren lassen sich die verschleißbedingten Vibrationen detektieren und ein rechtzeitiger Werkzeugtausch veranlassen, bevor es zu einem Ausfall kommt.
So können Schäden am zu bearbeitenden Bauteil, wie ausreißende Bohrlöcher oder im schlimmsten Fall sogar Schäden an der Maschine durch herumfliegende Teile vermieden werden.
Wie funktioniert Predictive Maintenance?
Die vorausschauende Wartung verknüpft Maschinendaten und Künstliche Intelligenz (KI), um den optimalen Zeitpunkt für Wartungsmaßnahmen zu bestimmen. Das Rückgrat dieser Vorgehensweise bilden Sensoren, IoT-Geräte und fortschrittliche Analysesoftware, die kontinuierlich Daten über den Zustand von Maschinen und Anlagen erfassen.
Der Prozess lässt sich in vier aufeinander bauende Schritte unterteilen. Jeder dieser Schritte erfordert spezifische Technologien und Fähigkeiten, die im Folgenden näher betrachtet werden.
1. Datenerfassung
Der erste Schritt ist die Erfassung relevanter Maschinendaten. Dazu werden die Maschinen mit Sensoren versehen, welche kontinuierlich Zustandsdaten sammeln und diese in das IT-Netzwerk einspeisen.
Typische Sensoren sind Vibrationssensoren, Thermografie-Kameras und Ultraschallmessgeräte, die Daten wie Schwingungen, Temperaturen, Druck oder Stromaufnahme in Echtzeit messen. Die erfassten Daten werden über industrielle Kommunikationsprotokolle wie OPC UA oder MQTT an eine zentrale Plattform übertragen, wo sie für die weitere Analyse bereitgestellt werden.
2. Datenanalyse
Im nächsten Schritt werden die gesammelten Daten mithilfe von Verfahren des maschinellen Lernens analysiert. Dabei kommen Algorithmen zum Einsatz, die Trends, Muster, Abweichungen und Anomalien in den Daten identifizieren.
Ziel ist es, Zusammenhänge zwischen verschiedenen Parametern zu erkennen, die auf einen bevorstehenden Ausfall hindeuten. Durch den Vergleich mit historischen Daten, technischen Spezifikationen und Echtzeit-Analysen können die KI-Modelle trainiert werden, um selbst kleinste Abweichungen vom Normalzustand zu erkennen. Diese Abweichungen können beispielsweise Temperaturanstiege oder Leistungsschwankungen sein, die auf einen sich anbahnenden Defekt hinweisen.
3. Vorhersage
Auf Basis der Datenanalyse werden Prognosemodelle entwickelt, die den zukünftigen Zustand der Maschinen vorhersagen. Dabei kommen trainierte Machine Learning-Algorithmen zum Einsatz, die Wahrscheinlichkeiten für potenzielle Ausfälle und die verbleibende Lebensdauer von Komponenten berechnen.
Diese Prognosen bilden die Grundlage für eine Risikobewertung, bei der die Auswirkungen eines möglichen Ausfalls auf die Produktion und die Kosten einer Reparatur oder eines Austauschs abgeschätzt werden. Anhand dieser Informationen lässt sich die Wartungsplanung optimieren, indem Instandhaltungsmaßnahmen gezielt zu dem Zeitpunkt durchgeführt werden, an dem sie den größten Nutzen bringen.
4. Optimierung
Nach der Umsetzung der geplanten Wartungsmaßnahmen, die auf den Vorhersagen basieren, erfolgt die Optimierung des gesamten Prozesses. Die Ergebnisse der durchgeführten Maßnahmen, wie beispielsweise Wartungsarbeiten, Teileersatz oder Aktualisierungen von Wartungsplänen, werden in einer Feedbackschleife in das System zurückgeführt.
Durch dieses kontinuierliche Lernen passen sich die Algorithmen und Modelle an die realen Gegebenheiten an, verbessern ihre Genauigkeit und Zuverlässigkeit und optimieren so das PdM-System stetig.
Die gewonnenen Erkenntnisse aus der prädiktiven Wartung haben weitreichende positive Auswirkungen auf den Instandhaltungsprozess. Durch die Analyse von Fehlerdaten und Wartungshistorien können spezifische Schwachstellen identifiziert und gezielt behoben werden.
Darüber hinaus ermöglicht die Anpassung von Wartungsintervallen an den tatsächlichen Zustand der Maschinen eine Optimierung der gesamten Instandhaltungsstrategie. Anstatt starrer, zeitbasierter Wartungspläne können so die Intervalle dynamisch und bedarfsgerecht auf Basis der Zustandsdaten angepasst werden.
Die technologischen Grundlagen
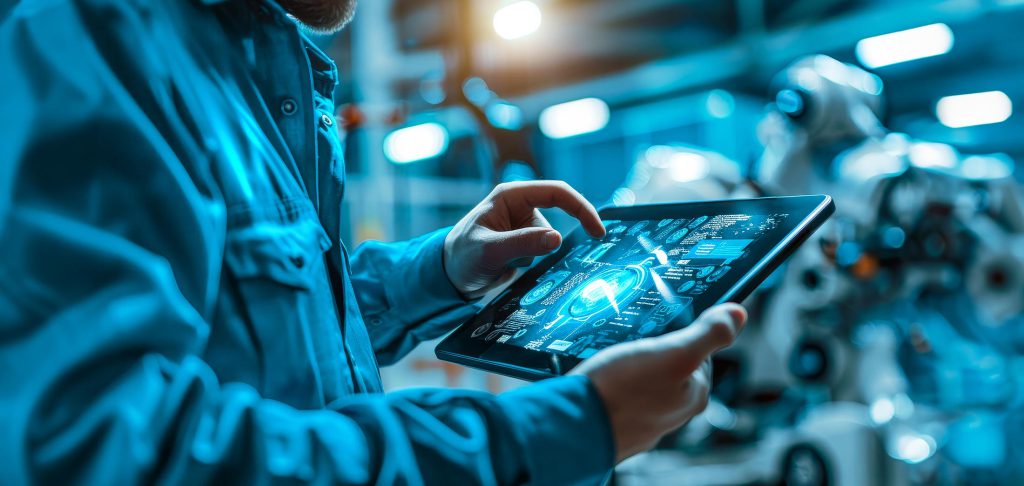
Die Effektivität von Predictive Maintenance basiert auf dem Zusammenspiel verschiedener Technologien. Während Sensorik, Internet of Things (IoT) und Machine Learning bereits als Kernkomponenten der Funktionsweise zum Ausdruck kamen, haben technologische Fortschritte in diesen Bereichen die Leistungsfähigkeit von PdM-Systemen weiter gesteigert.
Im Bereich des Machine Learnings haben sich Deep Learning-Modelle als bahnbrechend für PdM erwiesen. Convolutional Neural Networks (CNNs) zeichnen sich besonders durch ihre Fähigkeit aus, komplexe Muster in multidimensionalen Daten zu erkennen.
In der Praxis werden CNNs beispielsweise eingesetzt, um Anomalien in Vibrationsspektren von Rotationsmaschinen zu identifizieren. So können selbst subtile Veränderungen in den Schwingungsmustern, die auf einen beginnenden Lagerschaden hindeuten, frühzeitig erkannt werden.
Möchten Sie mehr über die Funktionsweise von Künstlicher Intelligenz erfahren? Dann werfen Sie doch einen Blick in unseren Leitfaden KI in der Industrie.
Diese fortschrittlichen Technologien bilden jedoch nur die Spitze des Eisbergs. Die vollständige Ausschöpfung des PdM-Potenzials erfordert zusätzliche Technologien für die Verarbeitung und Analyse der enormen generierten Datenmengen sowie für die lückenlose Zustandsüberwachung. Im Folgenden werden daher zwei weitere essenzielle technologische Grundlagen betrachtet.
Industrial IoT-Gateways
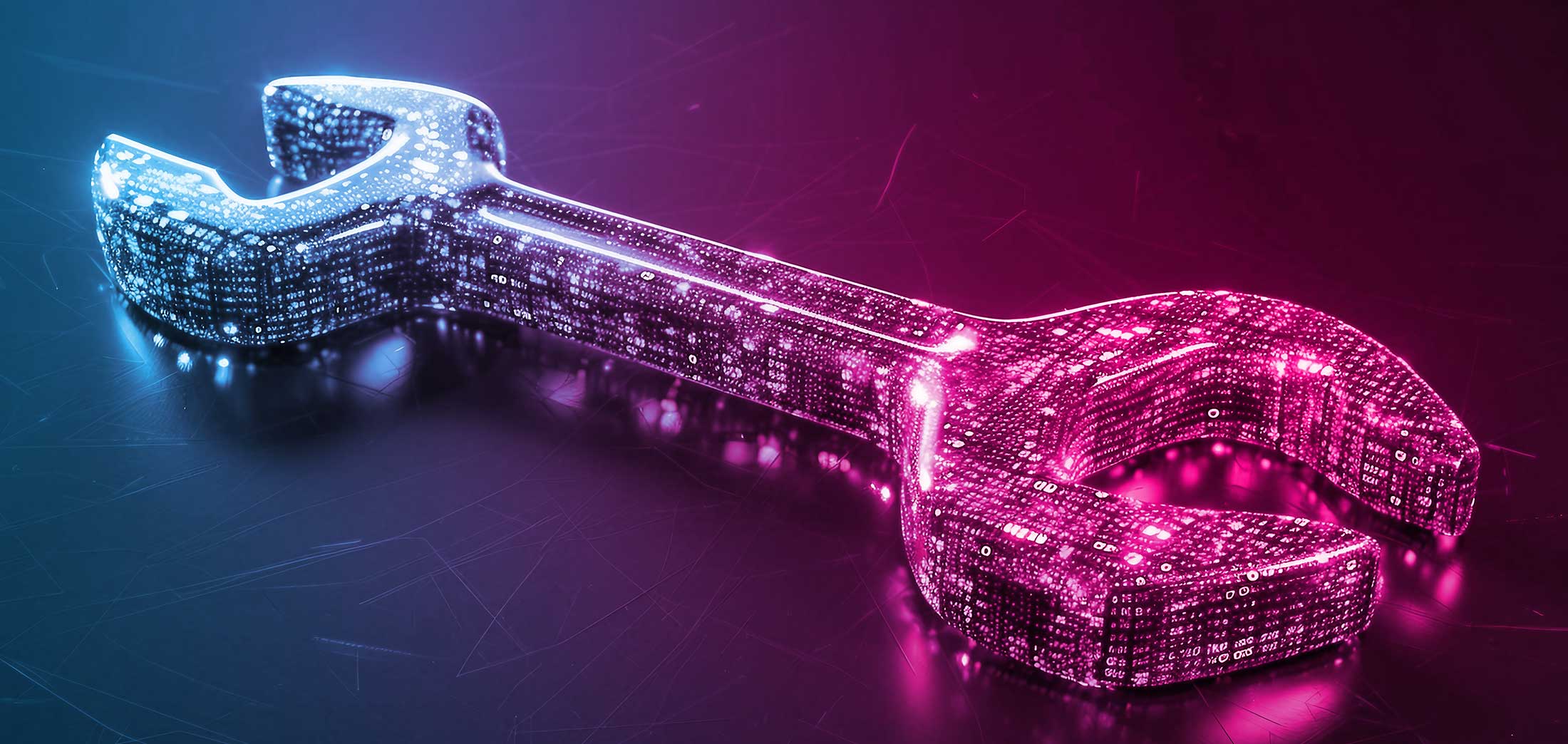
Eine große Herausforderung bei der Implementierung von Predictive Maintenance ist die Integration verschiedener Datenquellen. Um ein ganzheitliches Bild des Anlagenzustands zu erhalten, müssen Daten aus unterschiedlichsten Systemen und Quellen zusammengeführt und harmonisiert werden.
Die Komplexität dieser Aufgabe wird durch die Vielfalt der Datenformate noch verstärkt: Von einfachen Zahlenwerten über Textdateien und Log-Dateien bis hin zu komplexen strukturierten Daten wie JSON oder XML – die Heterogenität der Daten stellt erhebliche Anforderungen an die Integrationslösung.
Gateways des Industrial Internet of Things (IIoT) bieten einen leistungsfähigen Ansatz zur Bewältigung dieser Herausforderung. Diese spezialisierten Geräte fungieren als Brücke zwischen der physischen Welt der Maschinen und Sensoren und der digitalen Welt der Datenanalyse und Entscheidungsfindung.
IoT-Gateways ermöglichen eine nahtlose Kommunikation zwischen Maschinen, Sensoren, ERP-Systemen und externen Datenquellen wie Transport- und Logistikdaten. Ihre Kernfunktion besteht darin, die verschiedenen Datenströme zu übersetzen und zu vereinheitlichen, unabhängig von den zugrundeliegenden Systemen und Protokollen.
Ein wesentlicher Vorteil von Industrial IoT-Gateways liegt in ihrer Fähigkeit, Daten direkt an der Quelle zu verarbeiten und zu normalisieren. Dies bedeutet, dass die unterschiedlichen Datenformate bereits am Entstehungsort in ein einheitliches Format umgewandelt werden können.
Beispielsweise können proprietäre Binärformate oder unstrukturierte Textdateien in definierte Strukturen wie JSON oder XML überführt oder unstrukturierte Log-Dateien in strukturierte Datensätze umgewandelt werden. Diese Vorverarbeitung reduziert nicht nur die Datenmenge, die an zentrale Systeme übertragen werden muss, sondern erleichtert auch die nachfolgende Analyse erheblich.
Condition Monitoring
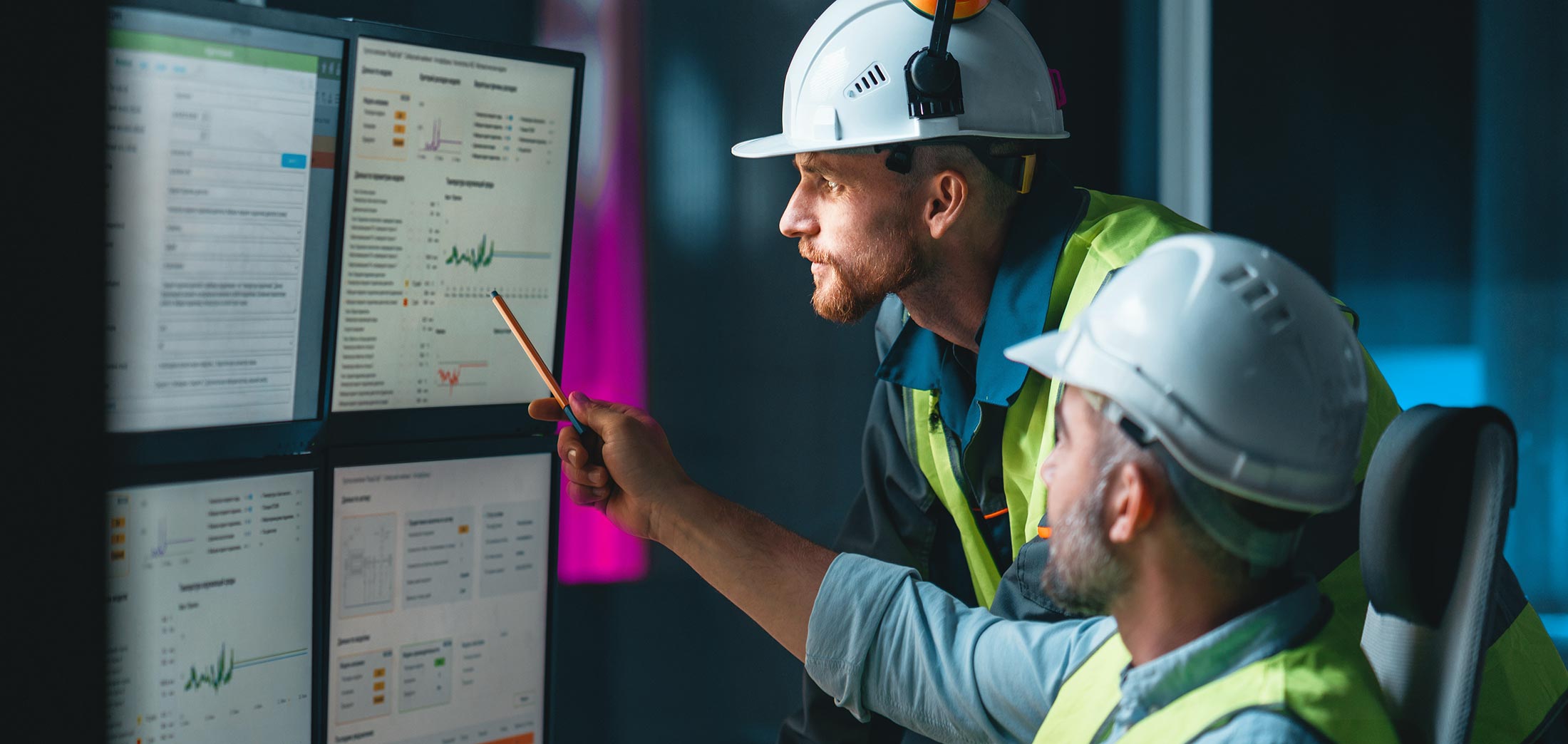
Condition Monitoring und Predictive Maintenance sind eng miteinander verknüpft, unterscheiden sich jedoch in ihrem Fokus und ihrer Zielsetzung. Condition Monitoring konzentriert sich auf die kontinuierliche Echtzeitüberwachung des Maschinenzustands und die Erkennung aktueller Probleme und Anomalien.
Hochentwickelte Sensortechnologien, insbesondere MEMS-Sensoren (Micro-Electro-Mechanical Systems), haben hierbei die Datenerfassung erheblich verbessert. Diese miniaturisierten Sensoren ermöglichen die simultane Messung multipler Parameter wie Vibrationen, Temperaturen und Beschleunigungen in einem hochintegrierten Format. Das Resultat ist eine deutlich höhere Granularität und Präzision in der Zustandsüberwachung, die selbst kleinste Veränderungen im Maschinenzustand detektiert und analysiert.
In Kombination mit IIoT-Plattformen schaffen diese Sensoren die Grundlage für eine umfassande Echtzeitüberwachung. Zentrale Systeme empfangen und verarbeiten anschließend die Datenströme mittels fortschrittlicher Analyseverfahren wie Frequenzanalysen oder Wavelet-Transformationen. Diese Techniken ermöglichen es, komplexe Signalmuster zu entschlüsseln und Anomalien frühzeitig zu identifizieren.
Zusammengefasst bildet Condition Monitoring das Fundament für Predictive Maintenance, indem es die Datenbasis für weiterführende Analysen und Vorhersagemodelle bereitstellt.
Use Case aus der Industrie
MaibornWolff entwickelte in Zusammenarbeit mit einem führenden Hersteller von Sicherheitstechnik eine Live-Monitoring-Plattform für vernetzte Gasmessgeräte. Das Projekt zielte darauf ab, in Industrieanlagen mit Gasförderwegen konstante Sicherheitslevel zu gewährleisten, indem heterogene Durchflussmesser auf einer zentralen Plattform vernetzt werden.
Use Case: Condition Monitoring
Ziel:
Entwicklung einer globalen Live-Monitoring-Plattform zur Visualisierung und Dokumentation von Messwerten und Statusänderungen vernetzter Gasmessgeräte.
Herausforderung:
- Verarbeitung hoher Datenvolumen ohne Alarmverluste
- Globale Alarmvisualisierung in weniger als 10 Sekunden
- Integration heterogener Durchflussmesser auf einer Plattform
Lösung:
- Entwicklung einer cloudbasierten Plattform mit Azure-Services (Kubernetes, Functions, IoT)
- Gateway-App für Android und iOS zur Geräteverbindung via Bluetooth
- Konfigurierbare Regeln und Grenzwerte für Ereignisauswertung
- Echtzeit-Standortübersicht und Statusmonitoring der Geräte
Besonderheiten:
- MVP-Entwicklung und Produktionsstart innerhalb von 3 Monaten
- Multimandantenfähigkeit für einfache Kundenintegration
Ergebnis:
Eine hocheffiziente, globale Monitoring-Lösung, die die Sicherheit in industriellen Umgebungen erhöht und den Einführungsaufwand für neue Kunden minimiert.
Projektdauer:
- 3 Jahre
Dieses Projekt veranschaulicht einen wichtigen Trend in der Industrie: Viele Unternehmen entscheiden sich zunächst für die Implementierung von Condition Monitoring als Vorstufe zur prädiktiven Instandhaltung.
Der Grund dafür liegt in der schrittweisen Herangehensweise an die Digitalisierung der Instandhaltung. Condition Monitoring ermöglicht es Unternehmen, zunächst eine solide Datenbasis aufzubauen und Erfahrungen mit der Echtzeitüberwachung zu sammeln, bevor sie in die komplexeren prädiktiven Analysen einsteigen.
Welche Vorteile bietet die vorausschauende Wartung?
Predictive Maintenance ermöglicht es Unternehmen verschiedener Branchen, von festgelegten Wartungsintervallen und reaktiven Reparaturen zu einer datengesteuerten, vorausschauenden Wartungsstrategie überzugehen.
Durch die Kombination von Echtzeitdaten aus dem Condition Monitoring mit fortschrittlichen Analysemethoden eröffnen sich neue Möglichkeiten für einen optimierten Anlagenbetrieb und eine effizientere Wartung. Dadurch entsteht eine Reihe konkreter Vorteile:
- Reduzierung ungeplanter Ausfallzeiten und Optimierung der Wartungsintervalle
- Erhöhte Kosten- und Betriebseffizienz
- Verlängerung der Lebensdauer von Anlagen
- Verbesserte Sicherheit und Compliance
- Optimierung der Ressourcennutzung
Ein bekanntes Beispiel für den Einsatz von Predictive Maintenance ist Siemens. Das Unternehmen nutzt diese Technologie in verschiedenen Bereichen, unter anderem in der Energieerzeugung und bei der Wartung von Gasturbinen.
Siemens setzt seine Senseye Predictive Maintenance-Lösung ein, um automatisch Verhaltensmodelle von Maschinen und Wartungsmitarbeitern zu erstellen. Diese Modelle sollen die Aufmerksamkeit und das Fachwissen der Nutzer auf die dringendsten Probleme lenken. Die Software analysiert Maschinen- und Wartungsdaten mithilfe von Machine-Learning-Algorithmen und präsentiert den Nutzern Benachrichtigungen innerhalb statischer, in sich geschlossener Fälle.
Kürzlich hat Siemens seine Predictive Maintenance-Lösung durch die Integration von generativer KI erweitert. Diese neue Funktionalität soll die vorausschauende Wartung gesprächsorientierter und intuitiver gestalten. Sie ermöglicht einen interaktiven Dialog zwischen dem Benutzer, der KI und Wartungsexperten, was den Entscheidungsprozess effizienter und effektiver machen soll.
Welche Herausforderungen gibt es bei der Implementierung?
Die Implementierung von Predictive Maintenance verspricht zwar erhebliche Vorteile, stellt Unternehmen jedoch auch vor komplexe Herausforderungen. Im Folgenden betrachten wir daher zwei Bereiche, die bei der Implementierung besondere Aufmerksamkeit erfordern: die Datenqualität und die Systemintegration.
Datenqualität
Bevor die gesammelten Daten für prädiktive Analysen genutzt werden können, müssen sie sorgfältig bereinigt und aufbereitet werden. Rohdaten, die von Sensoren und Maschinen erfasst werden, enthalten häufig Fehler, Lücken oder Inkonsistenzen. Diese Probleme können verschiedene Ursachen haben:
- Messfehler: Sensoren liefern aufgrund von Kalibrierungsproblemen, Umgebungseinflüssen oder Verschleiß ungenaue Werte.
- Kommunikationsprobleme: Datenübertragungsfehler führen zu fehlenden oder verfälschten Datenpunkten.
- Unvollständige Daten: Systemausfälle oder geplante Wartungsarbeiten führen zu Lücken in den Datensätzen.
- Formatinkonsistenzen: Daten aus verschiedenen Quellen liegen in unterschiedlichen Formaten oder Maßeinheiten vor.
Eine weitere Herausforderung bei der Datenqualität in Predictive Maintenance-Systemen ist der Umgang mit Anomalien und Ausreißern. Anomalien sind Datenpunkte, die signifikant vom erwarteten Verhalten oder Muster abweichen.
Sie können auf verschiedene Weise zustande kommen, z. B. durch Sensorfehler oder externe Einflüsse wie plötzliche Temperaturveränderungen. Falsch interpretierte Anomalien können sowohl zum Übersehen kritischer Maschinenprobleme als auch zu unnötigen Wartungsmaßnahmen führen.
Systemintegration
Die Integration von Predictive Maintenance in bestehende Produktionsumgebungen stellt Unternehmen vor technische und organisatorische Herausforderungen. In vielen Produktionsumgebungen sind Maschinen im Einsatz, die bereits seit Jahrzehnten zuverlässig ihre Dienste leisten.
Die älteren Anlagen verfügen jedoch nicht über die notwendige moderne Sensorik. Ihnen fehlen außerdem integrierte Kommunikationsschnittstellen für die Datenübertragung und sie verfügen oft nicht über die Möglichkeit, sich mit modernen Netzwerken zu verbinden.
Die Heterogenität der Maschinenparks verschärft diese Problematik zusätzlich. In einer typischen Produktionsumgebung finden sich Maschinen verschiedener Generationen, Hersteller und Technologien nebeneinander. Diese Vielfalt führt zu folgenden Problemen:
- Unterschiedliche Datenformate und -strukturen
- Inkompatible Kommunikationsprotokolle
- Variierende Steuerungssysteme und Benutzeroberflächen
- Uneinheitliche Wartungs- und Instandhaltungsanforderungen
- Divergierende Lebenszyklusphasen und Ersatzteilversorgung
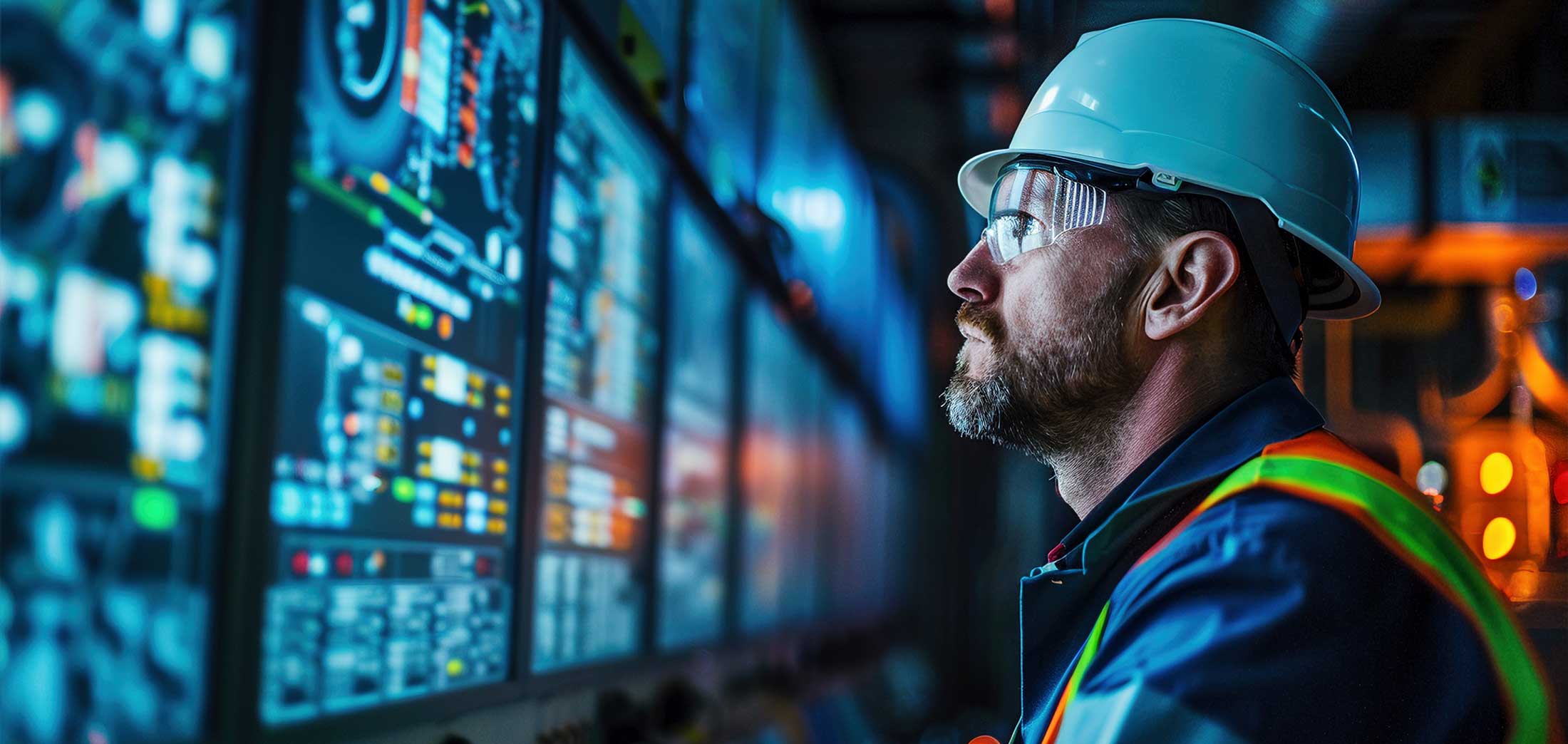
Die Integration all dieser verschiedenen Systeme in eine einheitliche Predictive Maintenance-Lösung erfordert oft aufwendige Anpassungen und Schnittstellenentwicklungen.
Zudem erschwert die Heterogenität die Entwicklung einheitlicher Analysemethoden und Vorhersagemodelle, da jede Maschinenart ihre eigenen spezifischen Betriebsparameter und Verschleißmuster aufweist. Doch selbst wenn eine Netzwerkverbindung möglich ist, können inkompatible Kommunikationsprotokolle die Datenübertragung erschweren.
Eine weitere Herausforderung ist die Implementierung des Predictive Maintenance Modells, bei dem Anomalien und Vorhersagen automatisiert auf Basis der Datengrundlage erkannt werden sollen. Dies erfordert eine Kombination aus Daten und Expertenwissen, das in Algorithmen überführt wird.
Um die Vorhersagegenauigkeit zu verbessern und mit unvollständigen oder verrauschten Daten umgehen zu können, werden die Algorithmen kontinuierlich anhand neuer Daten trainiert und optimiert. Die Entwicklung effektiver Modelle erfordert daher eine enge Zusammenarbeit zwischen Datenexperten, Domänenexperten und IT-Spezialisten, die ihr Fachwissen einbringen und in technisch umsetzbare Lösungen überführen.
Der Weg zur Implementierung von Predictive Maintenance
Die erfolgreiche Implementierung von Predictive Maintenance in Unternehmen erfordert strukturierte und kreative Lösungsansätze, insbesondere bei komplexen Herausforderungen wie der Bereinigung fehlerhafter Daten.
Um technische, aber auch organisatorische Hürden effektiv zu bewältigen, ist es entscheidend, bereits in der Initialphase des Projekts ein solides Fundament zu legen.
MaibornWolff bietet Ihnen dafür eine umfassende Beratung, die mit einer detaillierten Analyse Ihrer individuellen Anforderungen beginnt und Sie durch sämtliche Projektphasen begleitet. Unser Ansatz für ganzheitliche Lösungen umfasst dabei folgende Kernelemente:
1. Bedarfsanalyse und Strategieentwicklung
Zu Beginn wird eine umfassende Bedarfsanalyse durchgeführt, die bestehende Wartungsstrategien evaluiert und spezifische Ziele und KPIs identifiziert, die Sie mit Predictive Maintenance erreichen möchten.
Ein IIoT Solution Assessment ermittelt den aktuellen Reifegrad u.a. Ihrer Instandhaltungsprozesse und identifiziert Optimierungspotenziale Ihrer IT-Organisation. Dabei berücksichtigen wir auch organisatorische Faktoren wie Mitarbeiterkompetenzen und bestehende Datenmanagementpraktiken.
Bei der Entwicklung von Predictive Maintenance-Lösungen legen wir großen Wert auf Skalierbarkeit, um eine effiziente Übertragung auf verschiedene Werke oder Produktionslinien zu gewährleisten. Dadurch ermöglichen wir eine kosteneffiziente Implementierung in Ihrem gesamten Unternehmen.
Zu Beginn identifizieren wir gemeinsam mit Ihnen die spezifischen Herausforderungen und Potenziale, wie die Heterogenität des Maschinenparks oder die Auswirkungen und Anzeichen von Ausfällen. Durch eine gründliche Analyse der Problemstellung schaffen wir die Voraussetzungen für die Entwicklung einer individuellen Vorgehensweise, um Predictive Maintenance in Ihrem Unternehmen zu implementieren.
Basierend auf den gewonnenen Erkenntnissen erarbeiten wir passgenaue Konzepte, die sowohl technische als auch wirtschaftliche Aspekte berücksichtigen.
Unsere Experten unterstützen Sie bei der Erstellung einer detaillierten ROI-Rechnung, um den Nutzen der Predictive Maintenance-Lösung zu bewerten. So können Sie fundierte Entscheidungen treffen und die Vorteile der vorausschauenden Wartung optimal für Ihr Unternehmen einsetzen.
2. Integration und Auswahl von Technologie
Bei der Entwicklung einer prädiktiven Instandhaltung ist die Analyse der vorhandenen Datengrundlage ein entscheidender Schritt. Gemeinsam mit Ihnen ermitteln wir, ob alle erforderlichen Daten zur Umsetzung von Predictive Maintenance bereits vorhanden sind oder ob zusätzliche Sensoren integriert und weitere Datenquellen herangezogen werden müssen.
Je nach Anforderungen und Gegebenheiten kann Predictive Maintenance sowohl an einzelnen Maschinen als auch skalierbar im gesamten Werk implementiert werden. Für die Umsetzung an einer einzelnen Anlage können leistungsfähige Industrial PCs (IPC) eingesetzt werden, auf denen die Machine Learning Algorithmen direkt laufen. Dieser Ansatz ermöglicht eine gezielte Überwachung und Optimierung kritischer Maschinen, ohne dass eine komplette IIoT-Landschaft erforderlich ist.
Bei einer werksweiten Implementierung unterstützen wir Sie bei der Entwicklung einer umfassenden Datenstrategie. Gemeinsam entwerfen wir Maßnahmen zur Optimierung Ihrer Dateninfrastruktur und zur Sicherstellung von Datenverfügbarkeit und -qualität.
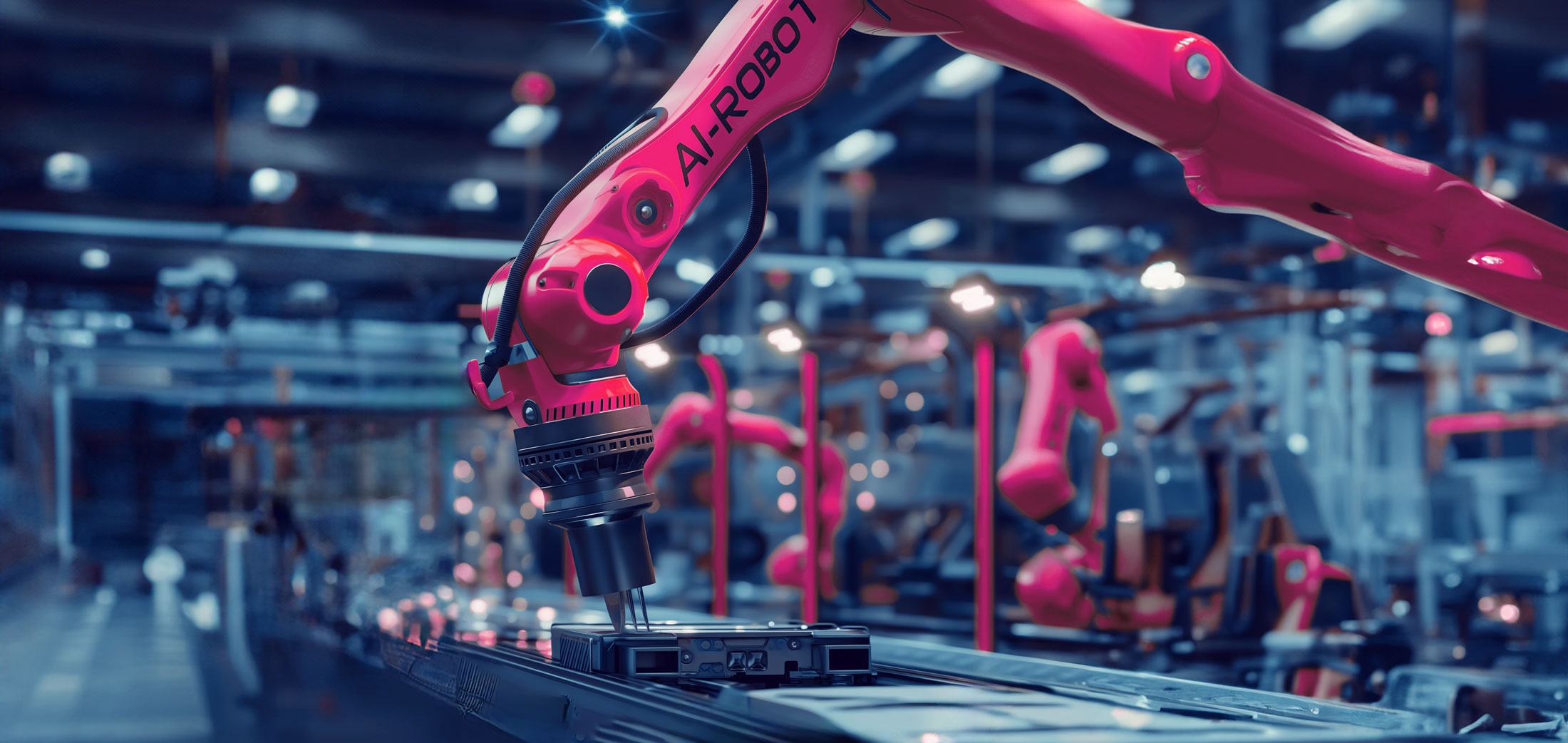
Die 10 Erfolgsfaktoren für Ihr KI-Projekt in der Produktion
Erfahren Sie, welche 10 Erfolgsfaktoren Sie bei der Einführung von KI in der Produktion beachten sollten.
Ein Schlüsselelement hierbei ist die Implementierung eines Unified Namespace, der eine konsistente und standardisierte Datenstruktur über alle Systeme hinweg gewährleistet. Dabei können moderne Ansätze wie Data Mesh genutzt werden, um die Datenverwaltung dezentral zu organisieren und Ihren Teams die Verantwortung für ihre eigenen Datenprodukte zu übertragen.
Unabhängig von der Skalierung legen wir bei der Identifikation und Installation der erforderlichen Sensoren und Datenerfassungssysteme besonderen Wert auf Zukunftsfähigkeit. Wir unterstützen Sie beim Aufbau und der Integration von IoT-Datenplattformen, die sich nahtlos in Ihre bestehenden IT-Systeme einfügen und gleichzeitig flexibel genug sind, um zukünftige Technologien zu integrieren.
Eine solide technische Basis ist entscheidend für die erfolgreiche Implementierung von Predictive Maintenance. Mehr über den Aufbau einer wiederverwendbaren und skalierbaren Daten-Architektur erfahren Sie in unserem Whitepaper „Unified Namespace“.
3. Implementierung von Predictive Maintenance
Bei der Implementierung von Predictive Maintenance setzt MaibornWolff auf einen strukturierten und iterativen Prozess, der auf einem tiefen Verständnis der komplexen Abläufe und Herausforderungen in Ihrem Unternehmen fußt.
Zu Beginn des Implementierungsprozesses unterstützen wir Sie bei der Auswahl der passenden ML-Plattform, die den Anforderungen Ihrer Predictive Maintenance-Anwendung gerecht wird. Dabei stehen Faktoren wie Skalierbarkeit, Integrationsfähigkeit und Benutzerfreundlichkeit im Fokus, um für eine nahtlose Einbindung in Ihre bestehende IT-Landschaft zu sorgen.
Anschließend widmen wir uns dem Training der Predictive Maintenance-Modelle. Hierbei kommen moderne Verfahren des maschinellen Lernens zum Einsatz, die anhand historischer Daten und Echtzeit-Informationen lernen, potenzielle Ausfälle und Wartungsbedarfe vorherzusagen. Durch umfangreiche Tests und eine erste Evaluation stellen wir sicher, dass die trainierten Modelle den gewünschten Anforderungen entsprechen und zuverlässige Ergebnisse liefern.
Um die Praxistauglichkeit der entwickelten Lösung zu validieren, starten wir zunächst mit einem Proof of Concept (PoC). Dieser ermöglicht es uns, die Modelle unter realen Bedingungen zu testen und wertvolles Feedback zu sammeln. Basierend auf den Erkenntnissen aus dem PoC nehmen wir gegebenenfalls Anpassungen vor, um die Leistungsfähigkeit und Zuverlässigkeit der Lösung weiter zu optimieren.
Nach erfolgreicher Validierung im PoC erfolgt die Überführung der Predictive Maintenance-Lösung in den Live-Betrieb. Während des Betriebs überwachen wir kontinuierlich die Vorhersagegenauigkeit der Modelle und gleichen die Ergebnisse mit der Realität ab.
Treten beispielsweise unvorhergesehene Ausfälle auf oder häufen sich Fehlalarme, nehmen wir gezielt Anpassungen an den Modellen vor, um die Prädiktionsgenauigkeit zu verbessern. Dieser iterative Prozess der Evaluation und Optimierung stellt sicher, dass die vorausschauende Wartung stets auf dem neuesten Stand bleibt und zuverlässige Ergebnisse liefert.
4. Schulung und Weiterbildung
Die erfolgreiche Implementierung von Predictive Maintenance erfordert ein nachhaltiges Schulungs- und Weiterbildungsprogramm für Mitarbeiter. Dieses zielt darauf ab, nicht nur technisches Wissen zu vermitteln, sondern auch eine Kultur der datengetriebenen Entscheidungsfindung zu etablieren.
Die Schulungen umfassen technische Aspekte wie den Umgang mit Sensoren und Analysesoftware, aber auch die Interpretation von Daten und deren Umsetzung in konkrete Handlungsempfehlungen. Mitarbeiter lernen, wie Predictive Maintenance in bestehende Prozesse integriert wird und wie sie zur kontinuierlichen Verbesserung des Systems beitragen können. Ziel ist es, Ihr Unternehmen zu befähigen, nach Abschluss unserer Beratung Predictive Maintenance selbstständig und effektiv zu nutzen.
5. Optimierung und Weiterentwicklung
Bei MaibornWolff verfolgen wir einen agilen Ansatz, bei dem die Optimierung der Umsetzungsstrategie stets Hand in Hand mit ihrer Weiterentwicklung geht. Durch regelmäßige Überprüfung und Verfeinerung der Vorhersagemodelle stellen wir sicher, dass die Prognosegenauigkeit kontinuierlich verbessert wird.
Dabei berücksichtigen wir auch sich ändernde Produktionsbedingungen, um die Relevanz und Effektivität des Systems aufrechtzuerhalten. Dieser iterative Prozess ermöglicht es uns, flexibel auf neue Herausforderungen zu reagieren und einen schnellen Return-on-Investment (ROI) zu erzielen.
Ein weiterer Schwerpunkt unseres Optimierungsprozesses liegt auf der Integration neuer Technologien. Wir evaluieren fortlaufend innovative Ansätze im Bereich der Datenanalyse, des maschinellen Lernens und der IoT-Technologien, um das Potenzial des Predictive Maintenance-Systems weiter auszuschöpfen. Dies kann beispielsweise die Implementierung fortschrittlicher Deep Learning-Algorithmen oder die Nutzung von Edge Computing für schnellere Datenverarbeitung umfassen.
Sobald die Predictive Maintenance-Lösung erfolgreich an einer Anlage implementiert ist und ihre Wirksamkeit unter Beweis gestellt hat, unterstützen wir Sie beim Rollout auf weitere Maschinen und Produktionslinien.
Dank der zuvor geschaffenen skalierbaren Strukturen lässt sich das System effizient auf andere Bereiche übertragen. Dabei passen wir die Lösung an die spezifischen Anforderungen der jeweiligen Maschinen an und berücksichtigen mögliche Unterschiede in den Datenquellen und Prozessabläufen.
Bringen Sie Predicitve Maintenance in Ihr Unternehmen!
Holen Sie sich jetzt eine individuelle Beratung für Ihr Unternehmen.
Use Case – Predictive Maintenance für Remote Access
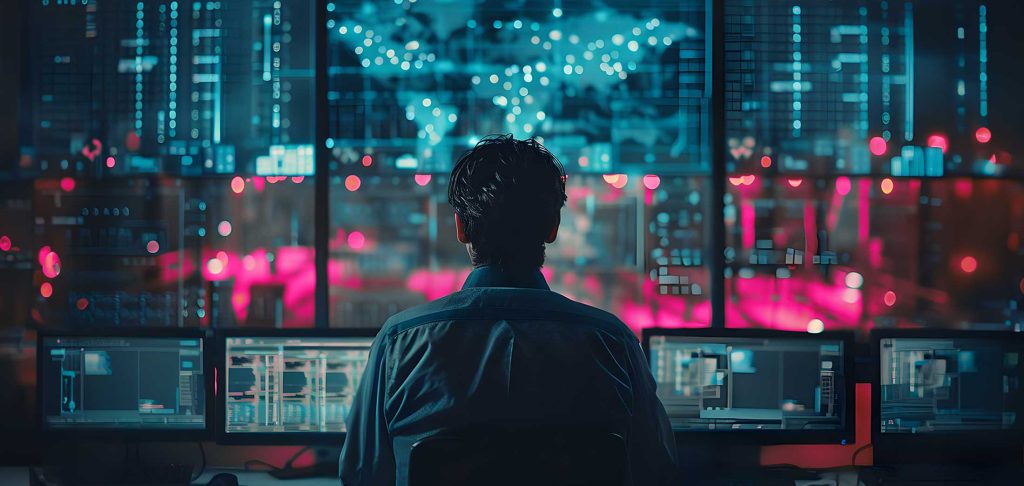
MaibornWolff unterstütze einen führenden Anbieter von Sensoren, Steuerungen und Systemen für die industrielle Automatisierung bei der Entwicklung einer fortschrittlichen Remote Access-Lösung. Diese Lösung ermöglicht nicht nur die Fernwartung von Anlagen und Maschinen, sondern bildet auch die Grundlage für die Implementierung von Predictive Maintenance. Durch den Remote-Zugriff können wichtige Maschinendaten und Sensormesswerte in Echtzeit erfasst und analysiert werden, um potenzielle Ausfälle frühzeitig zu erkennen und proaktiv Wartungsmaßnahmen einzuleiten.
Herausforderung
Die Herausforderung bestand darin, eine Remote Access-Lösung zu entwickeln, die sich durch einfache Bedienbarkeit von Wettbewerbsprodukten abhebt und nahtlos in die bestehende IoT-Plattform des Kunden integriert. Dabei mussten komplexe technische Anforderungen erfüllt und gleichzeitig eine hervorragende Benutzererfahrung gewährleistet werden.
Lösung
In enger Zusammenarbeit mit dem Kunden entwickelten wir eine Full Stack Cloud-Applikation sowie zwei auf RUST basierende Clients (Edge und Windows). Der Entwicklungsprozess umfasste:
- Eine vorgelagerte Konzeptphase zur Definition eines Minimum Viable Product (MVP)
- Implementierung in einem gemischten Team aus Kundenentwicklern und MaibornWolff-Experten
- Fokus auf einfache Bedienung und ausgefeiltes Fehler-Handling für optimale Benutzererfahrung
- Enge Zusammenarbeit mit dem Product Owner, UX/UI-Team und Plattform-Experten des Kunden
Ergebnis
Das Projekt resultierte in einer vollständig in die Kundenplattform integrierten Remote Access-Lösung, die auf der Hannover Messe 2024 präsentiert wurde. Die Lösung bietet:
- Effizienten Fernzugriff auf Anlagen und Maschinen
- Predictive Maintenance-Funktionen zur Vorhersage von Wartungsbedarf
- Intuitive Bedienung und verbesserte Fehlerdiagnose
- Optimierung von Wartungsprozessen und Minimierung von Ausfallzeiten
Die erfolgreiche Zusammenarbeit zwischen unserem Kunden und MaibornWolff demonstriert, wie spezialisierte technische Kompetenzen und ein nutzerzentrierter Ansatz zu innovativen Lösungen im Bereich Industrial IoT und Predictive Maintenance führen können.
Predictive Maintenance − Investition in die Zukunft
Für zukunftsorientierte Unternehmen bietet Predictive Maintenance ein enormes Potenzial zur Optimierung von Instandhaltungsprozessen und zur Steigerung der Wettbewerbsfähigkeit.
Als wichtiger Use Case von Smart Factory-Konzepten ebnet die vorausschauende Wartung den Weg zu einer intelligenten und vernetzten Produktion. Die gewonnenen Erkenntnisse und die Schaffung einer zukunftsfähigen Dateninfrastruktur dienen als wertvolle Grundlage für zukünftige Projekte und ermöglichen eine effizientere Umsetzung weiterer Industrie 4.0-Initiativen.
MaibornWolff unterstützt Sie bei der Beratung und Implementierung dieser Technologie, von der Konzeption über Pilotprojekte bis hin zur unternehmensweiten Einführung. Unser interdisziplinäres Team verfügt über umfassende Erfahrung in der Forschung und Entwicklung sowie in der Integration von Predictive Maintenance in bestehende Infrastrukturen. Wir begleiten Sie auf dem Weg zu individuellen Lösungen und bauen gemeinsam die Zukunftsfähigkeit Ihres Unternehmens aus.
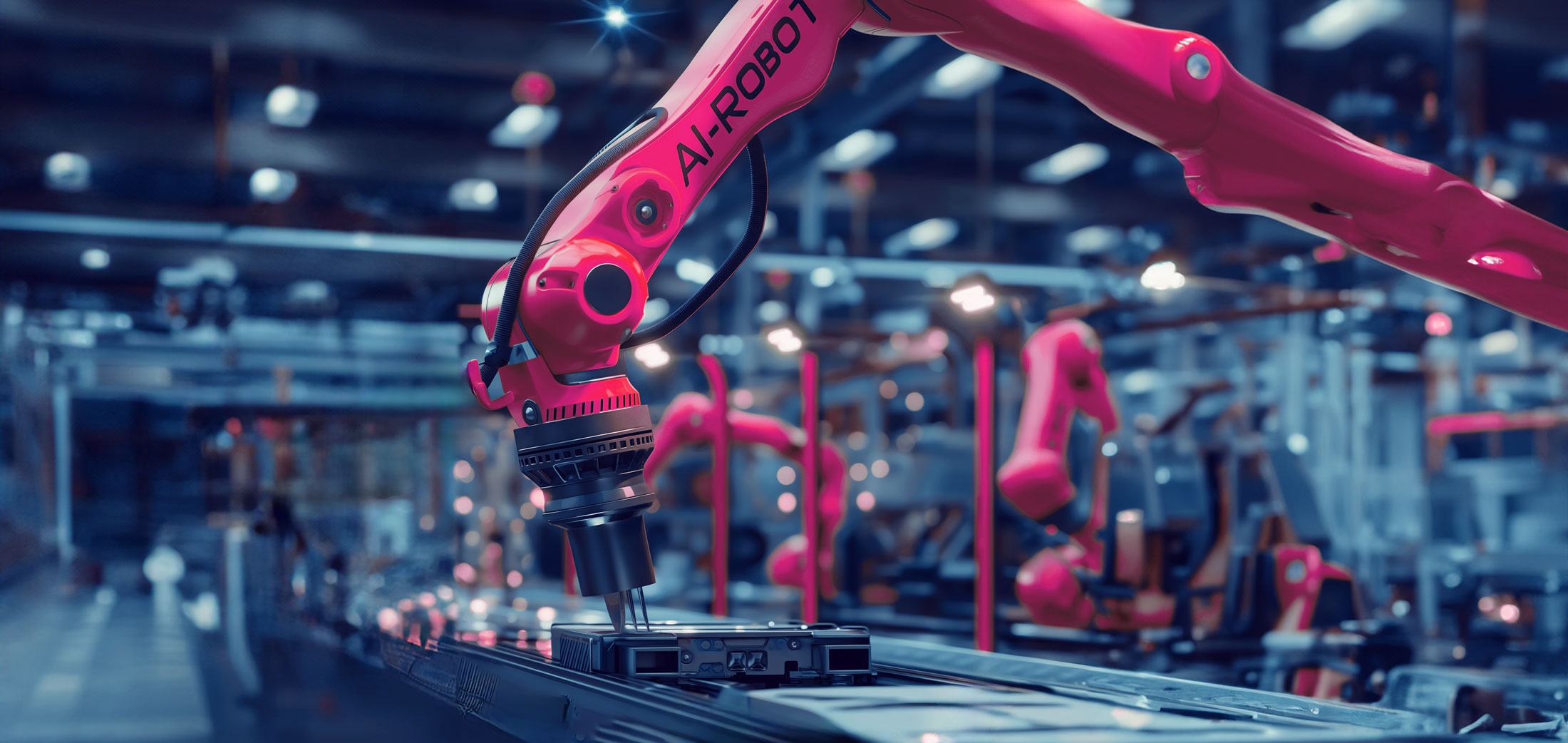
Die 10 Erfolgsfaktoren für Ihr KI-Projekt in der Produktion
Erfahren Sie, welche 10 Erfolgsfaktoren Sie bei der Einführung von KI in der Produktion beachten sollten.
FAQ: Häufig gestellte Fragen zur vorausschauenden Wartung
Predictive Maintenance ist eine innovative Instandhaltungsstrategie, die IoT-Sensoren und KI nutzt, um Maschinenzustände in Echtzeit zu überwachen. Sie ermöglicht bedarfsgerechte Wartungen und verhindert ungeplante Ausfälle durch frühzeitige Erkennung potenzieller Probleme.
Predictive Maintenance reduziert Stillstandzeiten, senkt Wartungskosten, verlängert die Maschinenlebensdauer und verbessert die Produktqualität. Es fördert Nachhaltigkeit durch effiziente Ressourcennutzung und bedarfsgerechte Ersatzteilproduktion.
Durch kontinuierliche Datenerfassung mittels Sensoren und Analyse durch KI-Algorithmen werden Anomalien frühzeitig erkannt. Dies ermöglicht präzise geplante Wartungsmaßnahmen und optimiert Instandhaltungsprozesse, wodurch Ausfälle vermieden werden.
Zentrale Technologien sind IoT-Sensoren zur Datenerfassung, Cloud-Computing für Datenspeicherung und -verarbeitung sowie KI-Algorithmen für Analyse und Prognosen. Diese Kombination ermöglicht eine effiziente und präzise vorausschauende Wartung.