Geschätzte Lesezeit 46 Minuten
Smart Factory – die Produktionsarbeit der Zukunft
Wir beleuchten die Rolle der intelligenten Fabrik im Kontext von Industrie 4.0, erläutern die technologischen Grundlagen und zeigen auf, wie Unternehmen den Weg zur Implementierung einer Smart Factory erfolgreich gestalten können. Sie erhalten einen detaillierten Einblick in die Zukunft der Fertigung und die damit einhergehenden technologischen Innovationen, Optimierungspotenziale und Herausforderungen für Ihr Unternehmen.
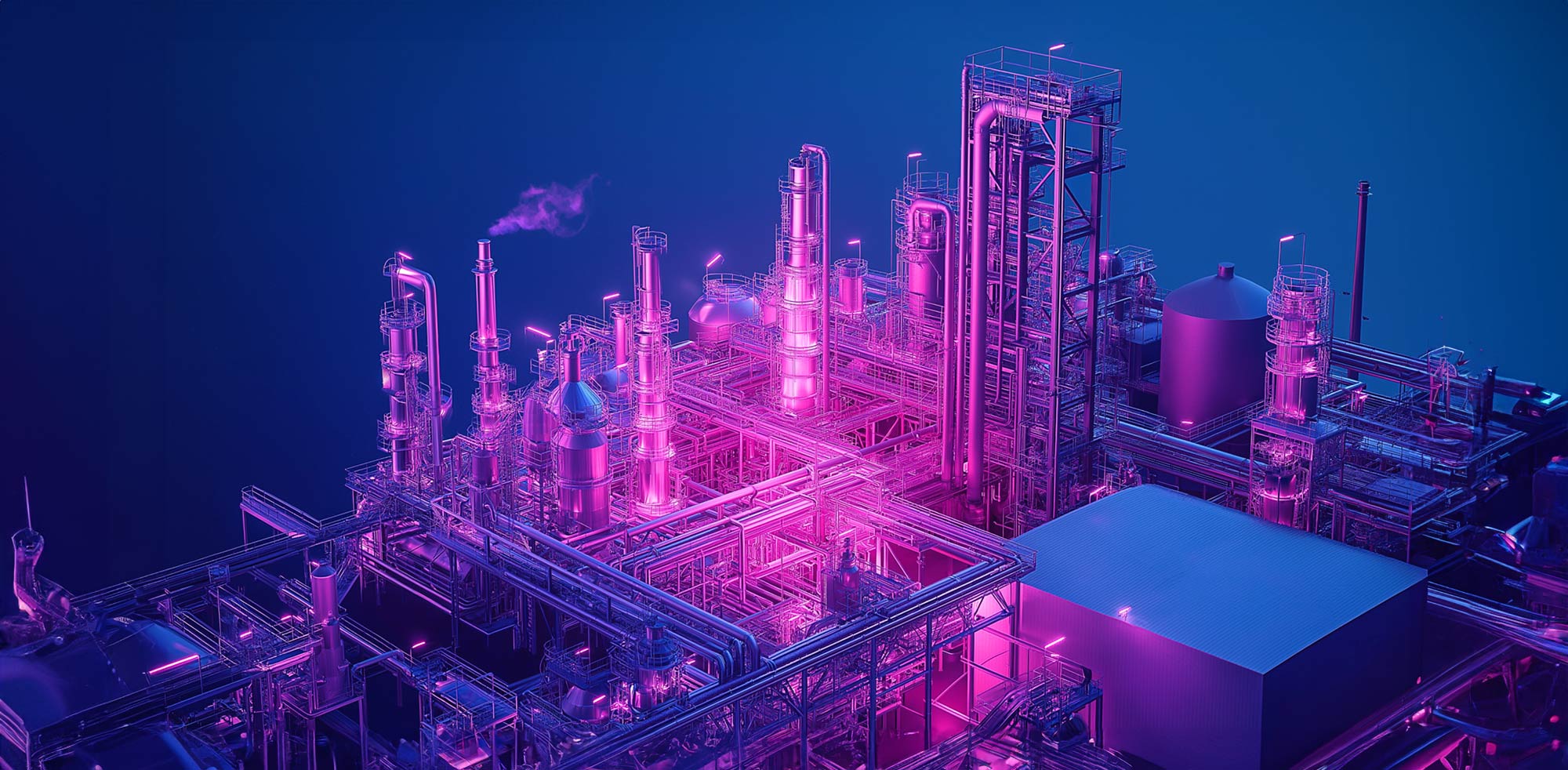
Overview
- Das Wichtigste in Kürze
- Was ist eine Smat Factory?
- Die Rolle der Smart Factory in der Industrie 4.0
- Vorteile und Potenziale für Unternehmen
- Die technologischen Grundlagen der Smart Factory
- Herausforderungen bei der Implementierung
- 5 Schritte zur Smart Factory mit MaibornWolff
- Use Case − Digitalisierung von Produktionskennzahlen
- Die Smart Factory als Erfolgsfaktor
- FAQ: Häufig gestellte Fragen zur Smart Factory
Die Digitalisierung revolutioniert die Industrie und ebnet den Weg für eine neue Generation der Fertigung. Im Zentrum der Entwicklung steht die Smart Factory, die intelligente Fabrik der Zukunft. Doch was genau verbirgt sich hinter diesem Begriff und welche Bedeutung hat die Smart Factory für Unternehmen?
Dieser Ratgeber bietet eine umfassende Einführung in das Konzept der Smart Factory. Wir beleuchten die Rolle der intelligenten Fabrik im Kontext von Industrie 4.0, erläutern die technologischen Grundlagen und zeigen auf, wie Unternehmen den Weg zur Implementierung einer Smart Factory erfolgreich gestalten können. Sie erhalten einen detaillierten Einblick in die Zukunft der Fertigung und die damit einhergehenden technologischen Innovationen, Optimierungspotenziale und Herausforderungen für Ihr Unternehmen.
Das Wichtigste in Kürze
Smart Factory
Definition:
Eine Smart Factory ist eine hochdigitalisierte Produktionsumgebung, die durch den Einsatz von Industrie 4.0-Technologien gekennzeichnet ist. Sie ermöglicht eine flexible und selbstoptimierende Produktion durch die Integration cyberphysischer Systeme.
Ziele:
- Steigerung der Produktionseffizienz
- Optimierung der Ressourcennutzung
- Verbesserung der Produktqualität
- Entwicklung neuer, datengetriebener Geschäftsmodelle
Technologien:
- Industrial Internet of Things (IIoT)
- Künstliche Intelligenz (KI)
- Big Data Analytics
- Cloud und Edge Computing
- Cyber-Physical Systems (CPS)
Vorteile:
- Reduzierung von Stillstandzeiten und Wartungskosten
- Erhöhung der Anlageneffizienz und -lebensdauer
- Verbesserte Produktionsplanung und Qualitätskontrolle
- Gesteigerte Wettbewerbsfähigkeit durch Flexibilität und Individualisierung
Beispiele:
- Predictive Maintenance zur vorausschauenden Wartung von Maschinen
- Echtzeitoptimierung von Produktionsprozessen durch KI-gestützte Analysen
- Digitale Zwillinge für Simulation und Optimierung von Produktionsanlagen
- Automatisierte Qualitätskontrolle durch Machine Vision und Deep Learning
Was ist eine Smat Factory?
Der technologische Fortschritt und die Digitalisierung verändern die industrielle Landschaft in Deutschland grundlegend. Um im globalen Wettbewerb bestehen zu können, müssen Unternehmen innovative Lösungen implementieren. Eine Schlüsselrolle für die Zukunftsfähigkeit des produzierenden Gewerbes spielt dabei das Konzept der Smart Factory.
Definition: Eine Smart Factory ist eine hochdigitalisierte und vernetzte Produktionsumgebung, in der Maschinen, Produkte und Menschen in Echtzeit miteinander kommunizieren. Sie nutzt moderne Technologien wie das Internet der Dinge (IoT), künstliche Intelligenz (KI) und Big Data, um Produktionsprozesse zu optimieren und flexibel auf Marktanforderungen zu reagieren.
Traditionelle Produktionsumgebungen unterscheiden sich weitgehend von Smart Factories in ihrer Herangehensweise an Wartung und Prozesssteuerung. In herkömmlichen Fabriken dominieren oft isolierte Systeme, die kaum miteinander kommunizieren. Die Wartung folgt meist starren, zeitbasierten Intervallen oder erfolgt reaktiv nach Ausfällen. Zusätzlich erschweren manuelle Steuerungsprozesse und begrenzte Echtzeitdatenerfassung eine flexible Anpassung an sich ändernde Produktionsbedingungen.
Im Gegensatz dazu zeichnet sich eine Smart Factory durch drei Kernelemente aus: vollständige Vernetzung, kontinuierliche Datenanalyse und selbstoptimierende Prozesse. Diese Eigenschaften bilden das Fundament für eine hocheffiziente Produktion. Durch die umfassende Vernetzung aller Komponenten entsteht ein digitales Ökosystem, in dem Maschinen, Sensoren und Steuerungssysteme nahtlos kommunizieren. Darauf aufbauend ermöglicht die kontinuierliche Datenanalyse in Echtzeit tiefgreifende Einblicke in den Produktionsprozess. Die Erkenntnisse fließen wiederum in selbstoptimierende Prozesse ein, die sich automatisch an veränderte Bedingungen anpassen. Folglich werden eine vorausschauende, bedarfsgerechte Wartung und eine agile Produktionsweise realisierbar.
Der Begriff „Smart Factory“ entstand im Rahmen der Industrie 4.0-Initiative, die 2011 als Zukunftsprojekt der deutschen Bundesregierung initiiert wurde. Diese vierte industrielle Revolution zielt darauf ab, die Wettbewerbsfähigkeit der deutschen Industrie durch die Integration cyberphysischer Systeme in Produktionsprozesse zu stärken. Die Smart Factory verkörpert dabei die Vision einer intelligenten, selbststeuernden Fabrik, die schnell auf Marktanforderungen reagieren kann.
Die Rolle der Smart Factory in der Industrie 4.0
Nach Dampfmaschine, Fließband und Computertechnologie markiert die Industrie 4.0 einen weiteren Meilenstein in der Entwicklung der Fertigungsindustrie. Im Mittelpunkt steht die intelligente Vernetzung von Menschen, Maschinen und industriellen Prozessen. Dabei werden Informations- und Kommunikationstechnologien mit Fertigungstechniken verschmolzen, um flexiblere Produktionsprozesse zu ermöglichen. Diese Entwicklung hat weitreichende Auswirkungen auf die gesamte Wertschöpfungskette, von der Produktentwicklung über die Fertigung bis hin zur Maschinenwartung.
Für den Wirtschaftsstandort Deutschland ist die Industrie 4.0 von enormer Bedeutung. Mit rund 15 Millionen Arbeitsplätzen, die direkt oder indirekt von der produzierenden Wirtschaft abhängen, bietet die Transformation viele Potenziale für Wachstum und Innovation. Durch die Implementierung von Industrie 4.0-Konzepten können deutsche Unternehmen ihre globale Wettbewerbsfähigkeit stärken und gleichzeitig neue, zukunftsfähige Geschäftsmodelle entwickeln.
Ein zentrales Element der digitalen Transformation ist die Smart Factory. Dort kommunizieren Bauteile eigenständig mit der Produktionsanlage. Maschinen koordinieren selbstständig Fertigungsprozesse und Service-Roboter unterstützen Menschen bei komplexen oder schweren Arbeiten. Diese intelligente Vernetzung vergrößert erheblich die Flexibilität und Effizienz in der Produktion.
Ein Beispiel für die praktische Anwendung von Industrie 4.0-Konzepten in einer Smart Factory ist die Instandhaltungsmethode Predictive Maintenance. Hierbei werden Maschinen und Anlagen mit Sensoren ausgestattet, die kontinuierlich Daten über den Betriebszustand erfassen. Mittels KI-gestützter Analyseverfahren können potenzielle Ausfälle frühzeitig erkannt und präventive Wartungsmaßnahmen eingeleitet werden. Das führt zu einer Reduzierung von Stillstandszeiten und einer Optimierung der Instandhaltungskosten.
Sie interessieren sich für die konkreten Vorteile und die Funktionsweise von Predictive Maintenance? Dann werfen Sie doch einen Blick in unseren Ratgeber „Predictive Maintenance − die Zukunft der Instandhaltung“.
Die Zukunft der industriellen Produktion wird maßgeblich durch die Weiterentwicklung und Verbreitung intelligenter Technologien geprägt sein. Dabei transformieren sich traditionelle, lineare Wertschöpfungsketten zu komplexen, vernetzten Wertschöpfungsnetzwerken in Smart Factories. Die gesteigerte Flexibilität in der Produktion und die präzisere Anpassung an individuelle Kundenwünsche sind wesentliche Vorteile dieser Transformation. Welche weiteren Chancen und Optimierungspotenziale die Implementierung einer Smart Factory für Unternehmen eröffnet, wird im folgenden Abschnitt näher erläutert.
Vorteile und Potenziale für Unternehmen
Die Implementierung einer Smart Factory eröffnet produzierenden Unternehmen vielfältige Chancen zur Steigerung ihrer Wettbewerbsfähigkeit. Tatsächlich erkennen 95 % der Unternehmen die Industrie 4.0 und die damit verbundenen Technologien als entscheidende Chance für ihre Zukunftsfähigkeit. Die digitale Transformation bewirkt nicht nur eine Optimierung des Kerngeschäfts, sondern auch die Erschließung neuer Märkte durch innovative Geschäftsmodelle und Produkte. Indem Smart Factories die Marktanforderungen nach Individualität, Anpassungsfähigkeit und Schnelligkeit adressieren, schaffen sie messbare Mehrwerte und positionieren Unternehmen optimal für die Herausforderungen des digitalen Zeitalters.
Effizienzsteigerung und Kostenreduktion
Smart Factories ermöglichen eine signifikante Effizienzsteigerung und Kostenreduktion durch die fortschrittliche Digitalisierung und Vernetzung der Produktionsprozesse. Ein Kernaspekt dabei ist die Optimierung der Produktionsabläufe anhand von Echtzeit-Datenanalyse und intelligenter Automatisierung.
Durch den Einsatz von IoT-Sensoren und fortschrittlichen Analysemethoden können Produktionsparameter kontinuierlich überwacht und automatisch angepasst werden. Dies führt zu einer Verbesserung der Produktqualität bei gleichzeitiger Reduzierung von Ausschuss und Nacharbeit. Zudem resultiert die präzise Steuerung der Produktionsprozesse in einer nachhaltigeren Nutzung von Ressourcen, was sich direkt in einer Senkung der Betriebskosten niederschlägt.
Ein weiterer entscheidender Faktor für die Effizienzsteigerung ist die Implementierung vorausschauender Wartungsstrategien. Durch Condition Monitoring, eine Schlüsseltechnologie der Smart Factory, werden Maschinen und Anlagen kontinuierlich überwacht. Hochentwickelte MEMS-Sensoren erfassen dabei simultan multiple Parameter wie Vibrationen, Temperaturen und Beschleunigungen. Die Daten werden in Echtzeit analysiert, um Anomalien frühzeitig zu erkennen und potenzielle Ausfälle vorherzusagen.
Ein Beispiel hierfür ist die Überwachung von Rotationsmaschinen mittels Vibrationssensoren. Durch die Analyse der Schwingungsmuster können selbst subtile Veränderungen, die auf einen beginnenden Lagerschaden hindeuten, frühzeitig erkannt werden. Das ermöglicht eine präzise Planung von Wartungsarbeiten, wodurch ungeplante Stillstandszeiten minimiert und die Gesamtanlageneffektivität (OEE) maximiert wird. Die Integration von Predictive Maintenance in die Smart Factory führt somit nicht nur zu einer Reduzierung der Wartungskosten, sondern auch zu einer Verlängerung der Maschinenlebensdauer.
Qualitätsverbesserung und Kundenzufriedenheit
Ein Kernaspekt der Qualitätsverbesserung in Smart Factories ist die Implementierung von In-Line-Qualitätskontrollen. Hierbei kommen hochauflösende Kamerasysteme und Sensoren zum Einsatz, die kontinuierlich den Produktionsprozess überwachen. Diese erfassen in Echtzeit Daten zu Produktmerkmalen wie Abmessungen, Oberflächenbeschaffenheit oder Farbgebung. Durch den Einsatz von Machine Learning-Algorithmen können selbst kleinste Abweichungen von den Sollwerten sofort erkannt und korrigiert werden. Das Resultat ist eine erhebliche Reduzierung von Ausschuss und Nacharbeit.
Eine besonders innovative Methode in diesem Bereich ist die Predictive Quality per Visual Inspection. Diese Technologie nutzt Deep Learning-Modelle, um potenzielle Qualitätsmängel bereits im Entstehungsprozess vorherzusagen. Beispielsweise können in der Automobilindustrie Lackierroboter mit KI-gestützten Kamerasystemen ausgestattet werden, die nicht nur aktuelle Fehler erkennen, sondern auch Muster identifizieren, die auf zukünftige Qualitätsprobleme hindeuten. Durch proaktive Anpassungen des Lackierprozesses können so sichtbare Mängel verhindert werden, bevor sie auftreten.
Darüber hinaus ermöglicht die umfassende Vernetzung in Smart Factories eine ganzheitliche Betrachtung der Qualitätsdaten entlang der gesamten Wertschöpfungskette. Durch die Integration von Lieferantendaten, Produktionsinformationen und Kundenrückmeldungen können Unternehmen Qualitätstrends analysieren und Verbesserungspotenziale identifizieren. Die datengetriebene Herangehensweise führt zu einer kontinuierlichen Optimierung der Produktqualität und letztendlich zu einer erhöhten Kundenzufriedenheit.
Agile Produktion und Marktanpassung
Smart Factories zeichnen sich durch ihre außerordentliche Flexibilität und Agilität aus, wodurch Unternehmen schnell auf veränderte Marktanforderungen reagieren können. Bestandteile dieser Anpassungsfähigkeit sind modulare Produktionslinien und fortschrittliche Steuerungssysteme, die eine rasche Umstellung der Fertigungsprozesse erlauben.
Ein wichtiger Faktor für die Agilität ist das Demand Forecasting mittels KI-gestützter Analysetools. Diese Systeme verarbeiten Echtzeitdaten aus verschiedenen Quellen wie Markttrends, Kundenpräferenzen und Lieferkettendynamiken, um präzise Nachfrageprognosen zu erstellen. Basierend auf den Vorhersagen kann dann die Produktionsplanung dynamisch angepasst werden.
Ein Beispiel für die praktische Anwendung dieser Konzepte ist die von MaibornWolff für Siemens entwickelte KI-gestützte Demand Prediction-Plattform. Diese Lösung liefert präzise Vorhersagen des Materialbedarfs in der industriellen Produktion. Durch die Integration von Maschinellem Lernen und fortschrittlichen Analysemethoden erstellt die Plattform Bedarfsprognosen mit hoher Genauigkeit. Das Ergebnis ist eine deutliche Optimierung der Lagerhaltung, Reduzierung von Überproduktion und eine verbesserte Liefertreue.
Die Integration von Advanced Planning and Scheduling (APS) Systemen bewirkt eine optimierte Ressourcenallokation und Produktionssequenzierung. Dadurch wechseln Unternehmen geschickt zwischen verschiedenen Produktvarianten, ohne Rüstzeiten oder Effizienzeinbußen in Kauf nehmen zu müssen. Die Agilität in der Produktion resultiert in kürzeren Markteinführungszeiten für neue Produkte und befähigt Unternehmen, schneller auf Kundenwünsche und Markttrends zu reagieren.
Ressourceneffizienz und Nachhaltigkeit
Die Integration einer Smart Factory eröffnet Unternehmen beachtliche Möglichkeiten zur Steigerung ihrer Ressourceneffizienz und zur Verbesserung ihrer ökologischen Bilanz. Durch den Einsatz fortschrittlicher Technologien können Produktionsprozesse präzise optimiert und der Materialverbrauch signifikant reduziert werden.
Zentrale Bestandteile dieser Optimierung sind intelligente Energiemanagementsysteme, die den Energieverbrauch in Echtzeit überwachen und steuern. Mithilfe von KI-gestützten Analysen lassen sich Produktionsprozesse energetisch optimieren, indem beispielsweise Lastspitzen vermieden und Energieflüsse gezielt gelenkt werden. Das führt nicht nur zu Kosteneinsparungen, sondern reduziert auch den CO2-Fußabdruck des Unternehmens.
Die Automatisierung von Wartungsplänen durch Predictive Maintenance-Systeme trägt ebenfalls zur Ressourcenschonung bei. Durch die bedarfsgerechte Wartung wird Verschleiß minimiert und die Lebensdauer von Maschinen und Komponenten verlängert, was den Bedarf an Ersatzteilen und damit den Ressourcenverbrauch reduziert.
Zudem ermöglichen Smart Factories eine präzisere Produktionsplanung und -steuerung, wodurch Ausschuss und Überproduktion minimiert werden. Die Anwendung von Konzepten der Green-IT in der Datenverarbeitung und -speicherung optimiert zusätzlich den ökologischen Fußabdruck der digitalen Infrastruktur.
Wie digital sind Sie bereits?
MaibornWolff unterstützt Sie dabei, das Potenzial Ihres Unternehmens durch Digitalisierungskonzepte voll auszuschöpfen. Vereinbaren Sie einfach ein unverbindliches Erstgespräch mit unseren Spezialisten, um gemeinsam Ihre digitale Zukunft zu gestalten.
Die technologischen Grundlagen der Smart Factory
Eine Smart Factory zeichnet sich durch die digitale Vernetzung aller Elemente der Wertschöpfungskette aus. Im Zentrum stehen dabei Smart Production und Smart Maintenance, die gemeinsam die Basis für selbststeuernde und autonome Unternehmensprozesse bilden. Smart Production optimiert die Wertschöpfungsprozesse, während Smart Maintenance für einen störungsfreien Produktionsablauf sorgt.
Diese Konzepte basieren auf fortschrittlichen technologischen Komponenten wie IIoT-Plattformen und künstlicher Intelligenz. Das Zusammenspiel der Technologien führt zu einer effizienten und individualisierten Produktion, wobei der Mensch in einer übergeordneten, strategischen Rolle agiert. In den folgenden Unterkapiteln werden die wichtigsten Verfahren und Technologien erläutert, die das Fundament einer Smart Factory sind und ihre Funktionsweise maßgeblich bestimmen.
Vernetzung und Echtzeit-Datenerfassung
In einer Smart Factory stellt das Industrial Internet of Things (IIoT) das Rückgrat für die Vernetzung aller Komponenten dar. Durch die Integration von Cyber-Physical Systems (CPS) werden physische Objekte nahtlos mit der digitalen Welt verbunden. Diese Systeme sorgen für eine kontinuierliche Echtzeit-Datenerfassung durch Sensoren an Maschinen und Produkten.
Smart Products, ausgestattet mit Informationsträgern, spielen eine Schlüsselrolle in der Smart Production. Sie „wissen“ jederzeit ihren exakten Status und Position im Produktionsprozess. So wird eine hohe Selbststeuerung und Flexibilität in der Fertigung erreicht. In der Smart Maintenance nutzen Maschinen die Vernetzung, um autonom Wartungsbedarfe zu melden und präventive Maßnahmen zu initiieren.
Elektronische Geräteakten (eDHR) ersetzen papierbasierte Dokumentationen und ermöglichen eine lückenlose, digitale Aufzeichnung aller relevanten Produktions- und Wartungsdaten. Die umfassende Vernetzung und Echtzeit-Datenerfassung bildet somit die Grundlage für eine anpassungsfähige und selbstoptimierende Produktion in der Smart Factory.
Datenanalyse und Entscheidungsfindung
Die zunehmende Vernetzung von Maschinen und Anlagen in Smart Factories generiert enorme Datenmengen. Um diese komplexen Systeme effizient zu steuern, ist künstliche Intelligenz (KI) für die Auswertung von Big Data in der Smart Production und Smart Maintenance von zentraler Bedeutung.
Insbesondere durch die Methode des maschinellen Lernens (ML) können komplexe Systemzustände klassifiziert und Korrelationen zwischen Prozessdaten und -ergebnissen identifiziert werden. Dadurch entsteht beispielsweise eine präzise Qualitätsprädiktion oder die Optimierung von Bearbeitungsparametern in der Produktion. Im Bereich der Smart Maintenance eröffnen sich Möglichkeiten wie die Vorhersage der Restlebensdauer von Komponenten, wodurch präventive Wartungsstrategien implementiert und ungeplante Ausfallzeiten minimiert werden können.
Ein bedeutendes Konzept in diesem Kontext ist der Digital Twin, der als virtuelle Repräsentation physischer Systeme fungiert. Dieser unterstützt Simulationen und Echtzeitanalysen und bietet zudem eine ganzheitliche Betrachtung der Produktionsprozesse. Daraus resultiert eine Optimierung von Abläufen und eine verbesserte Entscheidungsfindung.
Ergänzend dazu stellt Data Mesh als dezentrale Datenarchitektur eine flexible Nutzung und Verwaltung der Daten über verschiedene Unternehmensbereiche hinweg sicher. Der innovative Ansatz fördert die Datenverfügbarkeit und -qualität und ist Basis für eine optimale Verwertung der gesammelten Informationen.
Automatisierung und Robotik
Die rasante Entwicklung von Automatisierungstechnologien und Robotik verändert die Fertigungsindustrie. Im Jahr 2020 setzte bereits knapp jedes fünfte Unternehmen mit mehr als zehn Beschäftigten im verarbeitenden Gewerbe in Deutschland Industrie- oder Serviceroboter ein − ein deutlicher Indikator für den fortschreitenden Wandel in der Produktion.
In der Smart Production übernehmen Industrieroboter präzise und repetitive Aufgaben wie Schweißen, Montieren oder Verpacken. Durch ihre hohe Genauigkeit und Ausdauer steigern sie signifikant die Produktionseffizienz und -qualität. Kollaborative Roboter (Cobots) erweitern das Spektrum, indem sie sicher Seite an Seite mit menschlichen Mitarbeitern arbeiten und deren Fähigkeiten ergänzen.
Im Bereich Smart Maintenance kommen zunehmend mobile Roboter und Drohnen zum Einsatz. Diese autonomen Systeme, ausgestattet mit hochauflösenden Kameras und Sensoren, inspizieren schwer zugängliche oder gefährliche Bereiche. Sie erfassen kontinuierlich Zustandsdaten von Anlagen und ermöglichen so eine vorausschauende Wartung.
Dezentrale Datenverarbeitung
In Smart Factories spielen Cloud und Edge Computing komplementäre Rollen. Während Cloud-Lösungen für zentrale Datenanalysen und standortübergreifende Optimierungen sorgen, übernimmt Edge Computing die Echtzeitverarbeitung kritischer Produktionsdaten direkt vor Ort.
In der Smart Production sorgt diese Kombination für dynamische Fertigungsprozesse und schnelle Anpassungen an Marktanforderungen. Für die Smart Maintenance bietet Edge Computing den Vorteil, dass Maschinenzustände ohne Latenz überwacht und potenzielle Ausfälle frühzeitig erkannt werden können. Die Cloud fungiert hierbei als Plattform für tiefgreifende prädiktive Analysen und die Entwicklung optimierter Wartungsstrategien. Die hybride Architektur verbindet somit die Vorteile lokaler Reaktionsfähigkeit mit globaler Skalierbarkeit und Ressourceneffizienz.
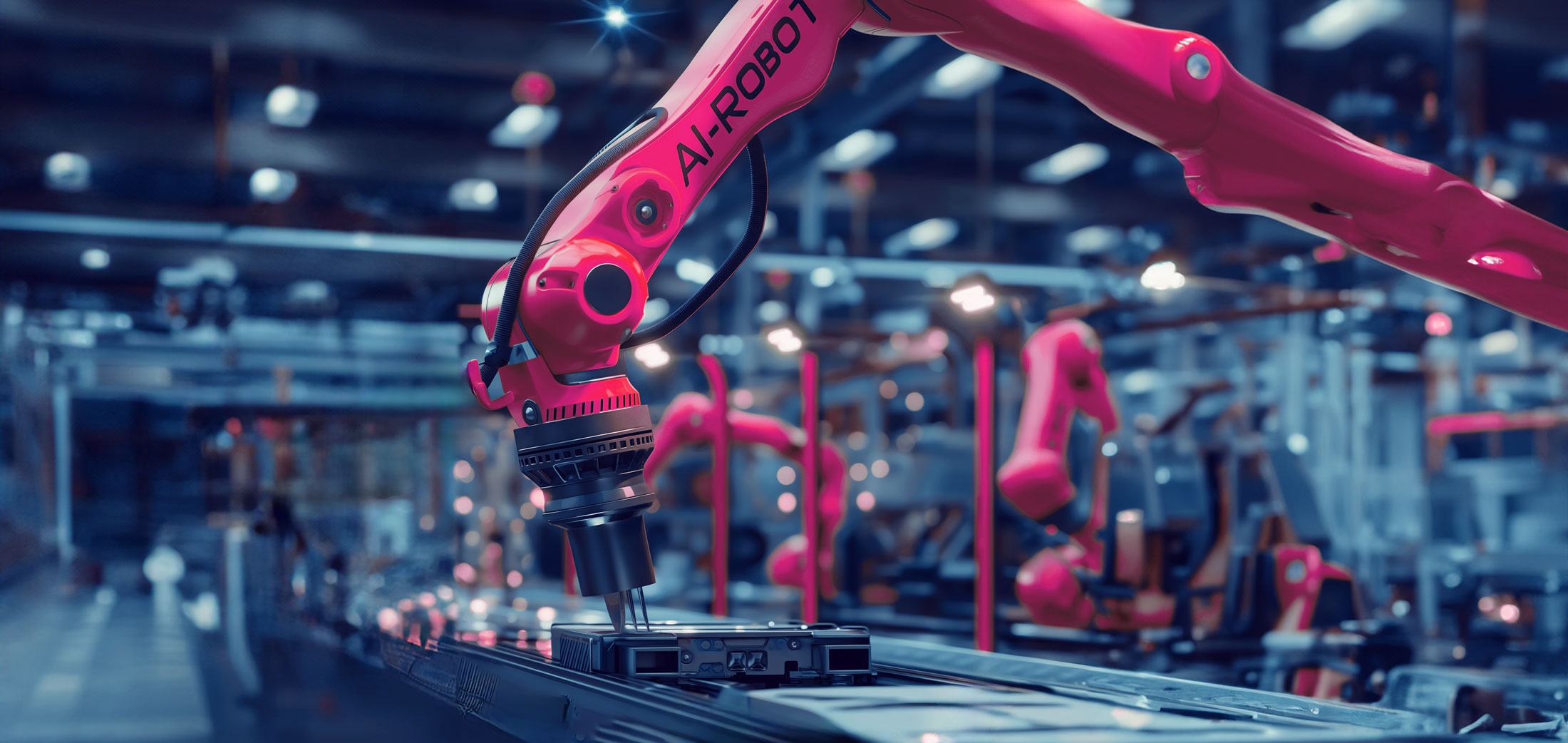
Die 10 Erfolgsfaktoren für Ihr KI-Projekt in der Produktion
Erfahren Sie, welche 10 Erfolgsfaktoren Sie bei der Einführung von KI in der Produktion beachten sollten.
Herausforderungen bei der Implementierung
Im Zuge von Industrie 4.0 erstreckt sich die Vernetzung weit über die Grenzen einzelner Fabriken hinaus. Es entstehen globale, digitale Ökosysteme, die neue Formen der Zusammenarbeit zwischen verschiedenen Akteuren ermöglichen − vom mittelständischen Zulieferer bis hin zu innovativen Start-ups. Die weitreichende Vernetzung schafft die Voraussetzungen für datengetriebene Geschäftsmodelle und trägt gleichzeitig zu einer ressourcenschonenden Produktion bei.
Die Implementierung von Industrie 4.0-Konzepten und Smart Factories stellt Unternehmen jedoch auch vor Herausforderungen. Mit der zunehmenden Digitalisierung und Vernetzung steigt die Komplexität der Systeme und es kommen Fragen bezüglich der Cybersecurity und Mitarbeiterqualifizierung auf. Damit eine Smart Factory ein Unternehmen zum Erfolg verhilft, müssen daher einige Rahmenbedingungen erfüllt werden, um folgende Herausforderungen zu überwinden.
Technologische Herausforderungen
Ein zentrales Problem ist die Gewährleistung der Interoperabilität zwischen heterogenen Systemen und Maschinen unterschiedlicher Generationen. Die Integration älterer Anlagen ohne moderne Sensorik oder Kommunikationsschnittstellen in ein vernetztes System erfordert oft aufwendige Anpassungen.
Ein kritischer Aspekt ist die IT-Sicherheit in vernetzten Produktionsumgebungen. Mit zunehmender Konnektivität steigt die Angriffsfläche für potenzielle Cyberattacken, was robuste Sicherheitskonzepte und kontinuierliche Überwachung unerlässlich macht.
Weitere technische Herausforderungen umfassen:
- Mangelnde Standardisierung von Schnittstellen und Protokollen
- Hohe Störanfälligkeit komplexer Systeme
- Notwendigkeit spezifischen technischen Know-hows
- Schaffung einer leistungsstarken und skalierbaren Infrastruktur
Ein häufiges Problem sind zudem Insellösungen und Datensilos, die eine effiziente Verknüpfung von Informationsquellen behindern. Obwohl es auf dem Markt vielzählige Softwares für die Instandhaltung und die Produktion gibt, ist die Vorbereitung der eigenen Datenlage eine wichtige Voraussetzung. In vielen Unternehmen fehlt es jedoch an den erforderlichen Daten zu Bestandshöhen oder technischen Spezifikationen, um derartige Softwares einsetzen zu können.
Organisatorische Herausforderungen
Die Implementierung einer Smart Factory erfordert tiefgreifende organisatorische Veränderungen, die weit über technische Aspekte hinausgehen. Ein effektives Change Management ist dabei von zentraler Bedeutung, um die Belegschaft in den Transformationsprozess einzubinden und eine nachhaltige Verankerung in der Unternehmenskultur zu gewährleisten. Die Integration von IT in den Produktionsprozess führt außerdem zu Änderungen der Arbeitsinhalte und erfordert somit eine Erweiterung der Qualifikationsprofile der Facharbeiter.
Weitere organisatorische Herausforderungen sind:
- Anpassung der Unternehmensstruktur an neue Kollaborationsformen
- Entwicklung agiler Arbeitsweisen und Entscheidungsprozesse
- Überwindung von Abteilungsgrenzen für eine enge Zusammenarbeit zwischen operativen und IT-Bereichen
- Verständnis, Kontrolle und Pflege des Systems und der zugehörigen Technologien
Die Akzeptanz und aktive Mitwirkung der Mitarbeiter sind für den Erfolg der Transformation unerlässlich. Dies erfordert eine frühzeitige und transparente Kommunikation der Digitalisierungsstrategie sowie eine Wissensvermittlung zu neuen Technologien und Trends und die Möglichkeit zur Mitgestaltung.
5 Schritte zur Smart Factory mit MaibornWolff
Die Digitalisierung eröffnet vielfältige Optimierungspotenziale in Wertschöpfungsprozessen, Effizienzsteigerung und flexibler Ressourcenallokation. Viele Unternehmen sehen sich jedoch mit erheblichen Herausforderungen konfrontiert. Grund dafür ist die Ausgangslage: isolierte Planungsprozesse, unstrukturiertes Datenmanagement und geringe Digitalisierungsgrade. Eine Smart Factory ist jedoch ein ganzheitliches Produktionssystem mit standardisierten Prozessen und Abläufen. Allerdings ist sie kein Produkt, das man kaufen kann, sondern das Ergebnis eines Transformationsprozesses. Wie schaffen es nun Unternehmen, diesen Wandel durchzuführen?
Dafür ist ein fundiertes Verständnis datenbasierter Ökonomie sowie organisatorischer Anforderungen unerlässlich. Für die Implementierung einer Smart Factory kommt es also auf eine gründliche Vorbereitung und wirkungsvolle Schritte an. Zur Identifikation dieser Schritte ist es notwendig, die Ausgangssituation, das Ziel sowie den Weg dahin klar zu formulieren. Genau das ist die Grundlage der Vorgehensweise von MaibornWolff, um Unternehmen auf dem Transformationspfad zur Smart Factory zu unterstützen. Unser Ansatz basiert dabei auf folgenden Kernelementen:
1. Bedarfsanalyse
Um den Weg zur Smart Factory zu ebnen, muss ein Unternehmen zunächst ein Bewusstsein dafür haben, wo es selbst in Sachen Digitalisierung steht. MaibornWolff führt dazu ein IIoT Solution Assessment durch, das den spezifischen Reifegrad sowie die Stärken und Schwächen des Unternehmens identifiziert. Die Aufnahme des Status quo umfasst die Analyse der bestehenden Ablauf- und Aufbauorganisation, der eingesetzten Technologien sowie der Mitarbeiterkompetenzen. Mittels Wertstrom- und Informationsflussanalysen werden in Kooperation mit den Unternehmensmitarbeitern externe Trends und interne Herausforderungen diskutiert. Die ganzheitliche und objektive Bewertung der Ausgangssituation ist die Bedingung für die Entwicklung zielgerichteter Maßnahmen und die Definition realistischer Ziele im Transformationsprozess zur Smart Factory.
Lesetipp: Erfahren Sie, wie die Analyse des digitalen Reifegrads durch FactoryPuls und MaibornWolff Unternehmen im Bereich Industrie 4.0 voranbringt. Diese Partnerschaft entwickelt maßgeschneiderte Implementierungsstrategien für Smart Factories und unterstützt bei der digitalen Transformation des Produktionsumfelds.
2. Strategieentwicklung
Die Ermittlung des Digitalisierungslevels von Prozessen und Maschinen ist entscheidend für eine zielgerichtete Strategieentwicklung zur Smart Factory-Implementierung. Hierbei werden Fähigkeiten wie die Objektlokalisierung und dezentrale Produktionssteuerung evaluiert, um Handlungsfelder zu identifizieren. Die daraus resultierende Roadmap umfasst konkrete Digitalisierungsmaßnahmen und den Einsatz innovativer Technologien, wobei die Integration von Komponenten für domänenübergreifende Interoperabilität besondere Beachtung findet.
Ein wichtiger Aspekt ist die Entwicklung offener Standards zur Gewährleistung nahtloser Kommunikation zwischen Systemen, Geräten und Anwendungen. Die Integration verschiedener Komponenten in digitale Ökosysteme wird dadurch realisiert, was die Voraussetzung für eine effiziente Smart Factory schafft.
Bei der Strategieentwicklung wird neben der zeitlichen Planung eine detaillierte Kosten-Nutzen-Analyse durchgeführt. Unsere Experten unterstützen Sie bei der Erstellung einer fundierten ROI-Rechnung. Diese liefert eine präzise Bewertung des Nutzens einer Smart Factory und bildet somit die Basis für informierte Entscheidungen und eine optimale Implementierung digitaler Konzepte in Ihrem Unternehmen.
3. Auswahl und Integration von Technologien
Bei der Implementierung von Smart Factory-Konzepten ist es entscheidend, dass Unternehmen nicht pauschal alles digitalisieren, sondern ein individuelles Optimum anstreben. MaibornWolff unterstützt Sie dabei, die für Ihr Unternehmen vielversprechendsten Industrie 4.0-Technologien zu identifizieren. Hierbei stehen Faktoren wie Skalierbarkeit, Integrationsfähigkeit und Benutzerfreundlichkeit im Fokus, um eine nahtlose Einbindung in Ihre bestehende IT-Landschaft zu gewährleisten.
Ein Schlüsselelement ist die Entwicklung einer umfassenden Datenstrategie. Diese besteht aus Maßnahmen zur Optimierung der Dateninfrastruktur sowie der Sicherstellung von Datenverfügbarkeit, einschließlich der Implementierung eines Unified Namespace für eine einheitliche Datenstruktur.
Zur Validierung der Praxistauglichkeit führen wir außerdem Proof of Concepts (PoC) durch. Typische Testszenarien könnten die Implementierung eines Condition Monitoring-Systems, die Integration von Predictive Maintenance-Algorithmen oder die Erprobung von Augmented Reality-Anwendungen für die Wartung umfassen. Die PoCs ermöglichen es, die Effektivität der ausgewählten Technologien unter realen Bedingungen zu evaluieren und gegebenenfalls Anpassungen vorzunehmen.
4. Schulung und Wissenstransfer
Die digitale Transformation in Richtung Smart Factory erfordert weit mehr als nur technologische Innovationen. Sie enthält tiefgreifende organisatorische Umstrukturierungen und die Etablierung neuer, digitaler Prozesse. Für den Erfolg ist es entscheidend, die Mitarbeiter aktiv in diesen Wandel einzubinden und eine zukunftsorientierte Unternehmenskultur zu schaffen.
Durch frühzeitige Information und Einbeziehung der Belegschaft wird sichergestellt, dass Potenziale voll ausgeschöpft werden und implementierte Maßnahmen ihre beabsichtigte Wirkung entfalten. Unser ganzheitlicher Ansatz umfasst sowohl die Vermittlung von Fachwissen zu Smart Factory-Konzepten als auch praktische Schulungen im Umgang mit neuen Technologien. Ziel ist es, eine nachhaltige Transformation zu gewährleisten, bei der technologische Innovationen und organisatorischer Wandel Hand in Hand gehen.
5. Optimierung und Weiterentwicklung
Die Implementierung einer Smart Factory ist ein kontinuierlicher, agiler Prozess, der weit über die initiale Einführung hinausgeht. Durch regelmäßige Überprüfung und Anpassung der Funktionsweisen und Mechanismen wird das System stetig optimiert. Dabei spielt die Integration neuer Technologien, wie beispielsweise Smart Devices für eine noch präzisere Datenerfassung und -analyse, eine zentrale Rolle.
Ein modularer Aufbau erlaubt es, die Smart Factory schrittweise auszubauen und neue Bereiche zu erschließen. Hierbei werden Erkenntnisse aus bereits optimierten Prozessen genutzt, um die Effizienz in anderen Produktionsbereichen zu steigern. Durch kontinuierliches Lernen und Anpassen der KI-Modelle verbessert sich die Vorhersagegenauigkeit für Wartungsbedarfe und Produktionsoptimierungen stetig. Der iterative Ansatz gewährleistet, dass die Smart Factory flexibel auf sich ändernde Marktanforderungen und technologische Innovationen reagieren kann.
Use Case − Digitalisierung von Produktionskennzahlen
Im Rahmen der Transformation zur Smart Factory unterstützte MaibornWolff Volkswagen bei der Entwicklung der iProcess-App, einer Lösung zur Digitalisierung von Produktionskennzahlen. Die App realisiert die Erfassung und Analyse von Produktionsdaten in Echtzeit. Zusätzlich demonstriert sie, wie die Integration fortschrittlicher Datenanalysetechnologien in bestehende Fertigungsprozesse deutliche Effizienzsteigerung und verbesserte Entscheidungsfindung in der Produktion bewirkt.
Die Herausforderungen bestanden darin:
- Komplexe Produktionsprozesse in einer benutzerfreundlichen App abzubilden
- Echtzeitdatenerfassung und -verarbeitung zu implementieren
- Eine nahtlose Integration in bestehende IT-Systeme zu gewährleisten
- Hohe Sicherheitsstandards und Datenschutzanforderungen zu erfüllen
In enger Zusammenarbeit entstand eine maßgeschneiderte Lösung:
- Konzeption und Implementierung einer intuitiven, webbasierten Anwendung
- Entwicklung einer robusten Backend-Infrastruktur für Echtzeitdatenverarbeitung
- Integration von Schnittstellen zu bestehenden Produktionssystemen
- Implementierung fortschrittlicher Sicherheitsmaßnahmen und Zugriffskontrollen
Die App lieferte signifikante Verbesserungen:
- Erhöhte Transparenz und Effizienz in der Produktion durch Echtzeitdatenvisualisierung
- Verbesserte Entscheidungsgrundlage für das Management dank präziser Kennzahlen
- Reduzierung manueller Dateneingaben und damit verbundener Fehler
- Flexiblere Anpassung an Produktionsänderungen durch dynamische Konfigurationsmöglichkeiten
Die Smart Factory als Erfolgsfaktor
Die Implementierung einer Smart Factory steigert die Wettbewerbsfähigkeit von Unternehmen durch umfassende Vernetzung und Digitalisierung der Produktion. Dies eröffnet innovative Geschäftsmodelle und Dienstleistungen, von denen insbesondere Start-ups sowie KMUs profitieren können. Die gesammelten Daten intelligenter Produkte und Maschinen ermöglichen die Entwicklung neuer Angebote und standortübergreifende Prozessoptimierungen.
Aber auch bei der Digitalisierung des Kerngeschäfts lässt sich der Erfolg anhand von klaren Kriterien wie Umsatzsteigerungen und Kostenreduktionen messen. Die verbesserte Kundenbindung und die Fähigkeit, sich dynamisch an evolvierende Kundenanforderungen anzupassen, unterstreichen die transformative Kraft der Digitalisierung und sichern eine nachhaltige Stärkung der Marktposition.
MaibornWolff unterstützt Sie mit interdisziplinären Kompetenzen und einem ganzheitlichen Ansatz auf dem Weg zu Ihrer intelligenten Fabrik. Von der Optimierung bestehender Prozesse bis hin zu ganzheitlichen Digitalisierungskonzepten entwickeln unsere Experten individuelle Lösungen. Gemeinsam erschließen wir die Potenziale einer Smart Factory für Ihr Unternehmen und schaffen Grundlagen für eine zukunftsgewandte Produktion.
Bringen Sie die Smart Factory in Ihr Unternehmen!
Vereinbaren Sie einfach ein unverbindliches Beratungsgespräch mit unseren Experten.
FAQ: Häufig gestellte Fragen zur Smart Factory
Eine Smart Factory ist eine hochdigitalisierte und vernetzte Produktionsumgebung, die durch den Einsatz von Technologien wie IIoT, KI und Big Data gekennzeichnet ist. Sie sorgen für eine flexible, effiziente und selbstoptimierende Produktion und Instandhaltung.
Smart Factories steigern die Produktionseffizienz, reduzieren Kosten und ermöglichen eine höhere Produktqualität. Sie bieten zudem verbesserte Flexibilität, kürzere Markteinführungszeiten und die Möglichkeit zur Entwicklung neuer, datengetriebener Geschäftsmodelle.
Der erste Schritt ist eine gründliche Analyse der bestehenden Prozesse und Technologien. Darauf aufbauend wird eine Strategie entwickelt, die schrittweise Implementierung von Technologien wie IoT-Sensoren, Datenanalyse-Plattformen und Automatisierungslösungen umfasst.